When we think of a “safe” parts washer solvent, we often conceive of the solvent regarding its safety for human use, particularly use by workers who apply the solvent in industrial settings. However, while human safety should be a primary concern when choosing a parts...
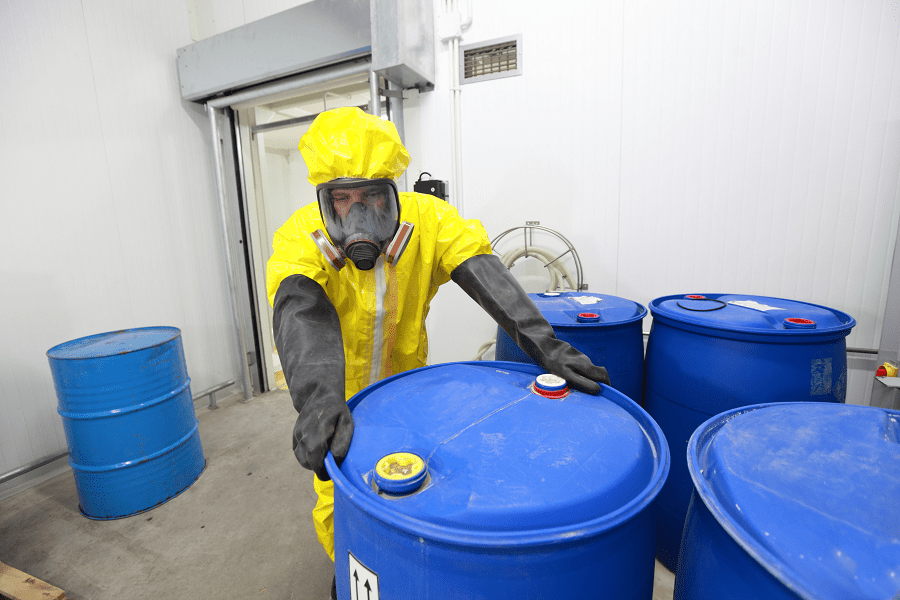