Making the switch to environmentally preferred solvents is a great way to protect the environment and your team’s health. But with an array of products labeled as ‘eco-friendly’ on the market, it can be difficult to determine which products are actually safe. At...
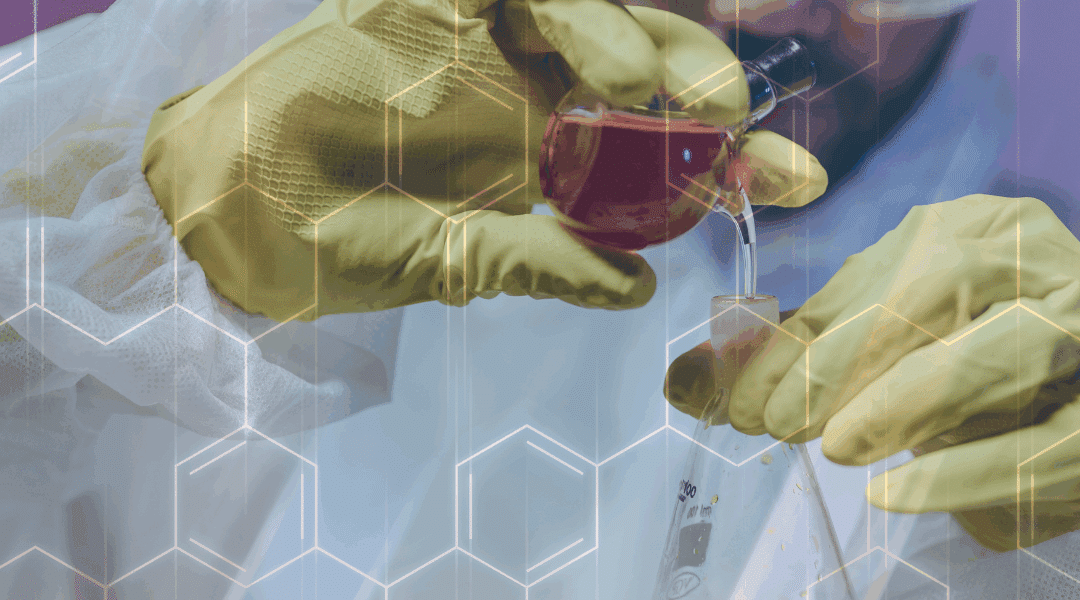