MIL-PRF-680B is officially replaced by MIL-PRF-680C
Effective April 15, 2010, MIL PRF 680B has been replaced with MIL-PRF-680C. The difference?
- 145° F Flashpoint
- Decent solvency
- SCAQMD and CARB compliant. Southcoast measured the VOC content at 17 grams/liter
- Compliant to MIL-PRF-680C Type V – this means approved for government/military use
- Evaporates residue free
Finally MIL PRF 680 gets VOC compliant
Call 800 886-8240 to request a FREE sample and experience the performance and safety of Ecolink 250-SS.
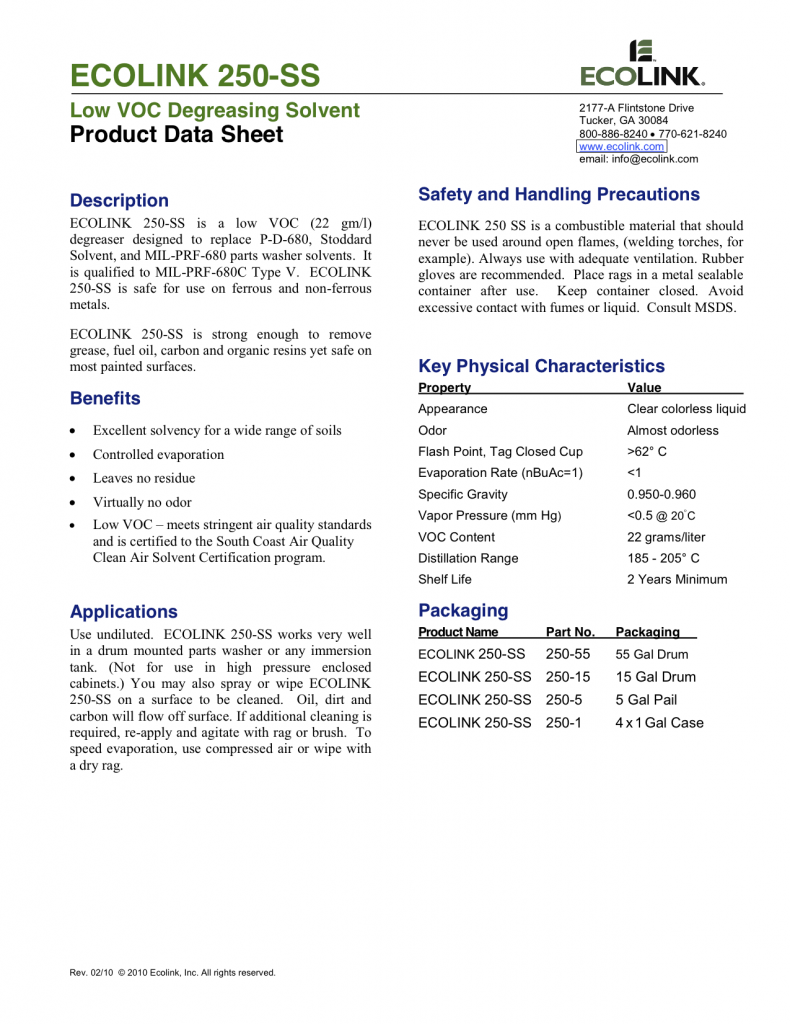
For more information on the evolution of MIL PRF 680 revision A to revision B to revision C, please visit:
/info/mil-prf-680c/
NOTE:This draft, dated 5 Feb 10, prepared by the U.S. Army Tank Automotive Research & Development Engineering Center, has not been approved and is subject to modification. DO NOT USE FOR ACQUISITION PURPOSES.
MIL-PRF-680C PROPOSED SUPERSEDING MIL-PRF-680B 26 October 2006
PERFORMANCE SPECIFICATION
DEGREASING SOLVENT
This specification is approved for use by all Departments and Agencies of the Department of Defense.
1. SCOPE
1.1 Scope. This specification covers degreasing solvent that consists of five types of petroleum distillates. The different types are referred to as “Stoddard solvent”, “141 degrees Fahrenheit (°F) (60.6 degrees Celsius (°C)) solvent”, “200°F (93.3°C) solvent”, “141°F d-limonene blended solvent” and “Low VOC solvent”. They are used for degreasing of machine parts in equipment maintenance.
1.2 Classification. Degreasing solvents are of the following types (see 6.2).
Type I – Low flash point (Stoddard solvent) (Military Symbol SD-1)
Type II – High flash point (Military Symbol SD-2)
Type III – Very high flash point (200°F) (Military Symbol SD-3)
Type IV – High flash point with citrus odor (Military Symbol SD-4)
Type V – Low VOC solvent (Military Symbol SD-5)
1.2.1 NATO classification:
Type I – S-752
Type II – S-753
Type III – S-760
Type IV – None
Type V – None
2. APPLICABLE DOCUMENTS
2.1 General. The documents listed in this section are specified in sections 3, 4, and 5 of this specification. This section does not include documents cited in other sections of this specification or recommended for additional information or as examples. While every effort has been made to ensure the completeness of this list, document users are cautioned that they must meet all specified requirement documents cited in sections 3, 4, and 5 of this specification, whether or not they are listed.
2.2 Government documents.
2.2.1 Specifications, standards, and handbooks. The following specifications, standards, and handbooks form a part of this document to the extent specified herein. Unless otherwise specified, the issues of these documents are those cited in the solicitation or contract.
STANDARD
FEDERAL
FED-STD-791 – Lubricants, Liquid Fuels and Related Products; Methods of Testing (FTM).
(Unless otherwise indicated, copies of the above specifications, standards, and handbooks are available from the Document Automation and Production Service, 700 Robbins Avenue, Building 4D, Philadelphia, PA 19111-5094.
2.2.2 Other Government documents, drawings and publications. The following other Government documents, drawings, and publications form a part of this document to the extent specified herein. Unless otherwise specified, the issues of these documents are those cited in the solicitation or contract.
ENVIRONMENTAL PROTECTION AGENCY (EPA)
EPA Method 420.1 – Methods for Chemical Analysis of Water and Wastes
Total Recoverable in Water and Solids.
EPA Method 3585 – Method for Waste Dilution for Volatile Organics.
EPA Method 8260B – Method for Volatile Organic Compounds by Gas
Chromatography/ Mass Spectrometry (GC/MS).
(Application for copies should be addressed to the US EPA Headquarters, 401 M Street SW, mail code 3204, Washington, DC 20460 or at http://www.epa.gov).
SOUTH COAST AIR QUALITY MANAGEMENT DISTRICT (SCAQMD)
SCAQMD Method 313 – Determination of Volatile Organic Compounds
(VOC) by Gas Chromatography/Mass Spectrometry (GC/MS).
(Application for copies should be addressed to the South Coast Air Quality Management District, 21865 Copley Drive, Diamond Bar, CA 91765 or at http://www.aqmd.gov)
2.3 Non-Government publications. The following document forms a part of this document to the extent specified herein. Unless otherwise specified, the issues of the documents which are DoD adopted are those listed in the issue of the DoDISS cited in the solicitation. Unless otherwise specified, the issues of these documents are those cited in the solicitation or contract.
AMERICAN SOCIETY FOR QUALITY (ASQ)
Z1.4 – Sampling Procedures and Tables for Inspection by Attributes (DoD
adopted).
(Application for copies should be addressed to the American Society for Quality, P.O. Box 3005, Milwaukee, WI 53201-3005 or at http://www.asq.org).
ASTM INTERNATIONAL
D 56 – Standard Test Method for Flash Point by Tag Closed Cup Tester
D 86 – Standard Test Method for Distillation of Petroleum Products at Atmospheric
Pressure
D 130 – Standard Test Method for Corrosiveness to Copper from Petroleum
Products by Copper Strip Test
D 156 – Standard Test Method for Saybolt Color of Petroleum Products (Saybolt
Chromometer Method)
D 235 – Standard Test Method for Mineral Spirits (Petroleum Spirits) (Hydrocarbon
Dry-Cleaning Solvent)
D 847 – Standard Test Method for Acidity of Benzene, Toluene, Xylenes, Solvent
Naphthas, and Similar Industrial Aromatic Hydrocarbons
D 1133 – Standard Test Method for Kauri-Butanol Value of Hydrocarbon Solvents
D 1296 – Standard Test Method for Odor of Volatile Solvents and Diluents
D 1298 – Standard Test Method for Density, Relative Density (Specific Gravity), or
API Gravity of Crude Petroleum and Liquid Petroleum Products by
Hydrometer Method
D 1353 – Standard Test Method for Nonvolatile Matter in Volatile Solvents for Use in
Paint, Varnish, Lacquer, and Related Products
D 2879 – Standard Test Method for Vapor Pressure-Temperature Relationship and
Initial Decomposition Temperature of Liquids by Isoteniscope
D 3257 – Standard Test Method for Aromatics in Mineral Spirits by Gas
Chromatography
D 4057 – Standard Practice for Manual Sampling of Petroleum and Petroleum
Products
D 4177 – Standard Practice for Automatic Sampling of Petroleum and Petroleum
Products
F 483 – Standard Test Method for Total Immersion Corrosion Test for Aircraft
Maintenance Chemicals
F 945 – Standard Test Method for Stress-Corrosion of Titanium Alloys by Aircraft
Engine Cleaning Materials
F 1110 – Standard Test Method for Sandwich Corrosion Test
(Application for copies should be addressed to ASTM International, 100 Barr Harbor Drive, West Conshohocken, PA 19428-2959 or at http://www.astm.org).
SOCIETY OF AUTOMOTIVE ENGINEERS (SAE)
AMS-QQ-A-250 – Aluminum and Aluminum Alloy, Plate and Sheet (DoD
adopted).
AMS 2470 – Anodic Treatment of Aluminum Alloys Chrome Acid Process
(DoD adopted).
AMS M 3171 – Magnesium Alloy, Processes for Pretreatment and Prevention
of Corrosion on (DoD adopted).
AMS 4377 – Magnesium Alloy, Sheet and Plate 3.0A1-1.0Zn-0.20Mn
(AZ31B-H24) Cold Rolled, Partially Annealed
AMS 4911 – Titanium Alloy Sheet, Strip, and Plate, 6AI-4V Annealed
AMS 5046 – Carbon Steel Sheet, Strip, and Plate, (SAE 1020 and 1025)
Annealed
(Application for copies should be addressed to the Society of Automotive Engineers, Inc., 400 Commonwealth Drive, Warrendale, PA 15096-0001 or at http://www.sae.org).
2.4 Order of precedence. In the event of a conflict between the text of this specification and the references cited herein, the text of this specification takes precedence. Nothing in this specification, however, supersedes applicable laws and regulations unless a specific exemption has been obtained.
3. REQUIREMENTS
3.1 Qualification. Solvents furnished under this specification shall be products that are authorized by the qualifying activity for listing on applicable qualified products list before contract award (see 4.2 and 6.3). Any change in the formulation of a qualified product will necessitate its requalification.
3.2 Materials. The hydrocarbon solvent shall be a virgin grade or recycled solvent derived from petroleum distillates, fraction from reclaiming and re-refining processes, or a mixture of these fractions. The d-limonene and hydrocarbon blended solvent is permitted as a Type IV solvent. The EPA exempt materials and hydrocarbon blended solvent is also permitted as a Type V solvent. The resultant solvent must be produced in such a manner as is necessary to meet the specified requirements.
3.3 Appearance. The solvent shall be clear and free from suspended matter and undissolved water when observed at a temperature between 60.1 and 78.1°F (15.6 and 25.6 °C).
3.4 Toxicity. The solvent shall have no adverse effects on human health when used as intended (see 6.1 and 6.6).
3.5 Carcinogenicity. The solvent shall contain no chemicals listed as carcinogens (see 6.7). Any carcinogenic components in the solvent in a concentration of 0.1 percent (%) or greater by weight (wt) or volume (vol) will be regarded as the presence of a carcinogen in the solvent.
3.6 Hazardous Air Pollutants. The solvent shall contain no chemicals listed as Hazardous Air Pollutants (HAPs) (see 6.7). Any HAP components in the solvent in a concentration of 1.0 percent (%) or greater by weight (wt) or volume (vol) will be regarded as the presence of a HAP in the solvent. The product containing less than 1 % of HAP shall be considered as a HAP free solvent. For carcinogenic HAPs see 3.5.
3.7 Physical and chemical property requirements. The solvents shall conform to the physical and chemical requirements in Table I when tested as specified in Table II.
TABLE I. Degreasing solvent properties.
Characteristics |
Type I |
Type II |
Type III |
Type IV |
Type V |
Flash point (pt) °C |
38-60 |
61–92 |
93-116 |
61–92 |
61–92 |
Flash point (pt) °F |
(100-140) |
(141-198) |
(200-241) |
(141-198) |
(141-198) |
Distillation, °C: |
|
|
|
|
|
Initial boiling pt., minimum (min) |
149 |
177 |
220 |
171 |
177 |
Dry point, °C, maximum (max) |
208 |
212 |
300 |
240 |
212 |
Kauri-Butanol value |
27 to 45 |
27 to 45 |
27 to 45 |
27 to 45 |
NR 4/ |
Aromatic content, vol %, max |
1 |
1 |
1 |
1 |
1 |
Total phenol content, parts per million (ppm), max |
0.5 |
0.5 |
0.5 |
0.5 |
0.5 |
Dichlorobenzene, milligrams per liter (mg/L), max Benzene, mg/L, max |
0.50.5 |
0.50.5 |
0.50.5 |
0.50.5 |
0.50.5 |
Tetrachloroethylene, mg/L, max |
0.7 |
0.7 |
0.7 |
0.7 |
0.7 |
Trichloroethylene, mg/L, max |
0.5 |
0.5 |
0.5 |
0.5 |
0.5 |
Apparent specific gravity,60/60°F |
0.754 to 0.820 |
0.754 to 0.820 |
0.754 to 0.820 |
0.754 to 0.820 |
0.754 to 0.820 |
Total chlorine content (ppm),Max |
100 |
100 |
100 |
100 |
100 |
Non-volatile residue, (mg/100 mL), max |
8 |
8 |
8 |
8 |
8 |
Color, min |
25 |
25 |
25 |
25 |
25 |
Odor 1/ |
Low & non-residual |
Low & non-residual |
Low & non-residual |
Low & non-residual |
Low & non-residual |
Corrosion, copper, max 2/ |
1b |
1b |
1b |
1b |
1b |
Sandwich corrosion, max |
1 |
1 |
1 |
1 |
1 |
Total immersion corrosion 3/ |
Pass |
Pass |
Pass |
Pass |
Pass |
Titanium stress corrosionAcidity |
No crackingNeutral |
No crackingNeutral |
No crackingNeutral |
No crackingNeutral |
No crackingNeutral |
Doctor test |
Negative |
Negative |
Negative |
Negative |
Negative |
Vapor pressure, millimeters of Mercury (mm Hg) @ 20oC, max |
7.0 |
2.0 |
0.4 |
2.0 |
1.0 |
Soil cleaning test, %, min |
85 |
85 |
85 |
85 |
85 |
VOC, g/l, max |
NR |
NR |
NR |
NR |
25 |
1/ Samples of MIL-PRF-680C, Type III, having satisfactory low odor characteristics
shall be used as reference standards.
2/ Test for three hours at 100 °C (212oF).
3/ See 4.4.2
4/ Not required
4. VERIFICATION
4.1 Classification of inspections. The inspection requirements specified herein are
classified as follows:
a. Qualification inspection (see 4.2)
b. Conformance inspection (see 4.3).
4.1.1 Inspection conditions. Unless otherwise specified, all inspections shall be performed in accordance the test conditions specified in 4.2.
4.2 Qualification inspection. The qualification inspection shall consist of all tests specified herein. Failure of any test shall be cause for rejection.
4.3 Conformance inspection. Conformance inspection shall consist of a sample for tests (see 4.3.2), samples for examination of filled containers (see 4.3.3), and the tests specified in Table II except for sandwich corrosion, total immersion corrosion, and titanium stress corrosion.
4.3.1 Lot. A lot shall consist of solvents from one batch or tank offered for delivery at one time. If material cannot be identified by batch or lot, a lot shall consist of not more than 10 000 gallons offered for delivery at one time (see 6.2).
4.3.2 Sampling for tests. Sampling of a lot for test purposes shall be in accordance with ASTM D 4057 or D 4177.
4.3.3 Sample for examination of filled containers. A random sample of filled unit containers and a sample of shipping containers fully prepared for delivery shall be selected from each lot of solvent in accordance with ASQ Z1.4.
4.4 Methods of inspection.
4.4.1 Tests. Tests shall be performed in accordance with the applicable methods specified in Table II and 4.4.2 through 4.4.3 to determine conformance with the requirements specified in 3.6.
TABLE II. Test methods for inspections.
Characteristic |
ASTM Methods |
Other Methods |
Flash Point |
D 56 |
|
Distillation |
D 86 |
|
Kauri-Butanol value |
D 1133 |
|
Aromatic content |
D 3257 |
|
Apparent specific gravity |
D 1298 |
|
Color |
D 156 |
|
Odor |
D 1296 |
|
Non-volatile residue |
D 1353 |
|
Copper Corrosion |
D 130 |
|
Sandwich corrosion |
F 1110 |
|
Total immersion corrosion |
F 483 |
|
Titanium stress corrosion |
F 945 |
|
Acidity |
D 847 |
|
Doctor test |
D 235 |
|
Vapor Pressure |
D 2879 |
|
Total phenol content |
|
EPA 420.1 |
Total dichlorobenzene content |
|
EPA 3585 and 8260B |
Total benzene content |
|
EPA 3585, 8260B |
Total trichloroethylene |
|
EPA 3585, 8260B |
Total tetrachloroethylene |
|
EPA 3585, 8260B |
Soil cleaning test |
|
FTM 791.7502 |
VOC test |
|
SCAQMD 313 |
4.4.2 Total immersion corrosion. The solvents shall not show any indication of staining, etching, pitting, or localized, or cause weight change to an average of three (3) test panels greater than that shown in Table III.
TABLE III. Alloy and maximum average weight loss.
Alloy |
Average of 3 panels wt. loss, max milligrams per square centimeter (mg/cm2/168 hrs) |
Magnesium (AZ 31B-H24) AMS 4377 surface treated in accordance with AMS-M-3171, Type III |
0.50 |
Aluminum, AMS-QQ-A-250, T3 surface, treatment in accordance with AMS 2470 |
0.15 |
Titanium, AMS 4911, 6AL-4V |
0.10 |
Steel, AMS 5046, Grade 1020 |
0.25 |
4.4.3 Soil cleaning test. The test shall be conducted according to the solvent soil test method described in the appendix. The soil used in this evaluation is MIL-PRF-10924 grease. The acceptable limit for each type of solvent is defined in Table I.
4.4.4 Total chlorine content. The total chlorine content of the solvent shall be determined by a gas chromatographic method, microcoulometric or by the use of a portable test kit for the quantitative analysis of chlorine (see 6.6). Nonconformance to Table I shall constitute failure of this test.
5. PACKAGING
5.1 Packaging. For acquisition purpose, the packaging requirements shall be as specified in the contract or order (see 6.2). When actual packaging of materiel is to be performed by DoD personnel, these personnel need to contact the responsible packaging activity to ascertain requisite packaging requirements. Packaging requirements are maintained by the Inventory Control Point’s packaging activity with the Military Department or Defense Agency, or within the Military Department’s System Command. Packaging data retrieval is available from the managing Military Department’s or Defense Agency’s automated packaging files, CD-ROM products, or by contracting the responsible packaging activity.
6. NOTES
(This section contains information of a general or explanatory nature that may be helpful, but is not mandatory.)
6.1 Intended use. These solvents are hydrocarbon-based solvents and are used as degreasers and cleaners for painted or unpainted metal parts. However, the compatibility between existing paints and solvents should be verified prior to use. It is recommended that these solvents should be used with an appropriate recirculated parts washer. No other commercial specification is available to cover these military applications.
6.1.1 Type I. Type I (Stoddard solvent) is intended for use where a low odor solvent with fast drying characteristics is desired. This solvent is currently defined as a flammable material due to its low flash point. It is recommended that the alternative solvents for Type I are Types II, III and IV. When Type I solvent is used indoors, ventilation should be sufficient to prevent the accumulation of vapors above allowable limits.
6.1.2 Type II. Type II (low odor with high flash point solvent) is intended for use where a solvent with a higher flash point is desired. It is recommended over Type I for safety and regulatory reasons. When Type II solvent is used indoors, ventilation should be sufficient to prevent the accumulation of vapors above allowable exposure limits.
6.1.3 Type III. Type III (low odor with very high flash point solvent) is intended to be used where confined atmospheric conditions require a cleaner that conforms to the Federal Government’s directives for reduced hazardous materials.
6.1.4 Type IV. Type IV (citrus odor with high flash point) is intended for use where a solvent with a high flash point and strong solvency is desired. This solvent is formulated with petroleum based hydrocarbon solvents and d-limonene additive. When Type IV solvent is used indoors, ventilation should be sufficient to prevent the accumulation of vapors above allowable exposure limits.
6.1.5 Type V. Type V (Low VOC solvent) is intended for use where solvent confined atmospheric conditions require a cleaner that conforms to the Federal and Local Government’s directives for reducing VOC of solvent.
6.2 Acquisition requirements. Acquisition documents must specify the following:
a. Title, number and date of this specification.
b. Type and quantity (see 1.2. and 4.3.1).
c. Issue of DODISS to be cited in the solicitation, and if required, the specific issue of individual documents referenced (see 2.2.1 and 2.3).
d. Packaging requirements (see 5.1)
6.3 Qualification. With respect to products requiring qualification, awards will be made only for products which are at the time of award of contract, qualified for inclusion in Qualified Product List QPL No. 680 whether or not such products have actually been so listed by that date. The attention of the contractors is called to these requirements, and manufacturers are urged to arrange to have the products that they propose to offer to the Federal Government tested for qualification in order that they may be eligible to be awarded contracts or purchase orders for the products covered by this specification.
6.3.1 Specification preparing activity. Information and instructions regarding qualification inspection under this specification may be obtained from the Department of the Army, TACOM-TARDEC, ATTN: AMSRD-TAR-E/268, 6501 E. 11 Mile Road, Warren, MI 48397-5000.
6.4 International standardization. Certain provisions of this specification are the subject of international standardization agreement (NATO STANAG 1135, ANNEX C). When amendment, revision, or cancellation of this specification is proposed which would affect or violate the international agreement concerned, the preparing activity will take appropriate reconciliation action through international channels, including departmental standardization offices, if required.
6.5 Disposal actions. Disposal of this product should be in accordance with local, state and Federal regulations. Care should be taken to avoid mixing used MIL-PRF-680 with other waste materials, especially those containing halogenated solvents. However, these solvents can be recycled instead of disposal.
6.6 Material Safety Data Sheets. Contracting officers will identify those activities requiring copies of completed Material Safety Data Sheets (MSDSs) prepared in accordance with FED-STD-313. The pertinent Government mailing addresses for submission of data are listed in FED-STD-313; and 29 CFR 1910.1200 requires that the MSDS for each hazardous chemical used in an operation must be readily available to personnel using the material. Contracting officers will identify the activities requiring copies of the MSDS (see 3.4 and 4.4.4).
6.7 Definitions.
6.7.1 Carcinogens. The Occupational Safety and Health Administration (OSHA) definition of carcinogens are those chemicals / processes appearing in lists 1, 2A, and 2B of the International Agency for Research on Cancer (IARC) 1/; substances known to be carcinogenic and occupational exposures associated with a technological process known to be carcinogenic by the National Toxicology Program (NTP) Report on Carcinogens (latest annual report) 2/; and OSHA regulated carcinogens.
6.7.2. Hazardous Air Pollutant (HAP). HAP is defined as any substance listed under Section 112 of the Clean Air Act or its modifications. The text of the Clean Air Act, listed pollutants and modifications are kept by the Environmental Protection Agency (EPA) and are accessible through the website: http://www.epa.gov
1/ Copies of these volumes may be found in medical libraries or through the World Health Organization, 1211 Geneva 27, Switzerland.
2/ Copies may be obtained from the Public Health Service, National Toxicology Program, Public Information Office, P.O. Box 12233, MD B2-04, Research Triangle Park, NC 27709 or at http://ntp-server.niehs.nih.gov
6.8 Subject term (key word) listing.
d-limonene
d-limonene/hydrocarbon blended solvent (type IV)
Mineral Spirits
Naphtha
Petroleum Spirits (USA)
Stoddard Solvent (type I)
141 F Solvent (type II)
200 F Solvent (type III)
Low VOC Solvent (type V)
6.9 Changes from previous issues. Marginal notations are not used in this revision to identify changes with respect to the previous issue due to the extensiveness of the changes.
Custodians: Army – AT Preparing Activity:
Air Force – 68 Navy – AS Army – AT
(Project 6850-2010-007)
Review Activities:
Army – AV, EA, MD1, MI, MR, SM
Air Force – 03, 11, 50
Navy – MC, SH
DLA – GS, GS3, DP
DTRA – DS
GSA/GSS – 7FLE
MISC – MP
NOTE: The activities listed above were interested in this document as of the date of this document.
MIL-PRF-680B is Officially Replaced by MIL-PRF-680C
/in Ecolink News/by Industrial DegreasersMIL-PRF-680B is officially replaced by MIL-PRF-680C
Effective April 15, 2010, MIL PRF 680B has been replaced with MIL-PRF-680C. The difference?
For more information on the evolution of MIL PRF 680 revision A to revision B to revision C, please visit:
/info/mil-prf-680c/
NOTE:This draft, dated 5 Feb 10, prepared by the U.S. Army Tank Automotive Research & Development Engineering Center, has not been approved and is subject to modification. DO NOT USE FOR ACQUISITION PURPOSES.
MIL-PRF-680C PROPOSED SUPERSEDING MIL-PRF-680B 26 October 2006
PERFORMANCE SPECIFICATION
DEGREASING SOLVENT
This specification is approved for use by all Departments and Agencies of the Department of Defense.
1. SCOPE
1.1 Scope. This specification covers degreasing solvent that consists of five types of petroleum distillates. The different types are referred to as “Stoddard solvent”, “141 degrees Fahrenheit (°F) (60.6 degrees Celsius (°C)) solvent”, “200°F (93.3°C) solvent”, “141°F d-limonene blended solvent” and “Low VOC solvent”. They are used for degreasing of machine parts in equipment maintenance.
1.2 Classification. Degreasing solvents are of the following types (see 6.2).
Type I – Low flash point (Stoddard solvent) (Military Symbol SD-1)
Type II – High flash point (Military Symbol SD-2)
Type III – Very high flash point (200°F) (Military Symbol SD-3)
Type IV – High flash point with citrus odor (Military Symbol SD-4)
Type V – Low VOC solvent (Military Symbol SD-5)
1.2.1 NATO classification:
Type I – S-752
Type II – S-753
Type III – S-760
Type IV – None
Type V – None
2. APPLICABLE DOCUMENTS
2.1 General. The documents listed in this section are specified in sections 3, 4, and 5 of this specification. This section does not include documents cited in other sections of this specification or recommended for additional information or as examples. While every effort has been made to ensure the completeness of this list, document users are cautioned that they must meet all specified requirement documents cited in sections 3, 4, and 5 of this specification, whether or not they are listed.
2.2 Government documents.
2.2.1 Specifications, standards, and handbooks. The following specifications, standards, and handbooks form a part of this document to the extent specified herein. Unless otherwise specified, the issues of these documents are those cited in the solicitation or contract.
STANDARD
FEDERAL
FED-STD-791 – Lubricants, Liquid Fuels and Related Products; Methods of Testing (FTM).
(Unless otherwise indicated, copies of the above specifications, standards, and handbooks are available from the Document Automation and Production Service, 700 Robbins Avenue, Building 4D, Philadelphia, PA 19111-5094.
2.2.2 Other Government documents, drawings and publications. The following other Government documents, drawings, and publications form a part of this document to the extent specified herein. Unless otherwise specified, the issues of these documents are those cited in the solicitation or contract.
ENVIRONMENTAL PROTECTION AGENCY (EPA)
EPA Method 420.1 – Methods for Chemical Analysis of Water and Wastes
Total Recoverable in Water and Solids.
EPA Method 3585 – Method for Waste Dilution for Volatile Organics.
EPA Method 8260B – Method for Volatile Organic Compounds by Gas
Chromatography/ Mass Spectrometry (GC/MS).
(Application for copies should be addressed to the US EPA Headquarters, 401 M Street SW, mail code 3204, Washington, DC 20460 or at http://www.epa.gov).
SOUTH COAST AIR QUALITY MANAGEMENT DISTRICT (SCAQMD)
SCAQMD Method 313 – Determination of Volatile Organic Compounds
(VOC) by Gas Chromatography/Mass Spectrometry (GC/MS).
(Application for copies should be addressed to the South Coast Air Quality Management District, 21865 Copley Drive, Diamond Bar, CA 91765 or at http://www.aqmd.gov)
2.3 Non-Government publications. The following document forms a part of this document to the extent specified herein. Unless otherwise specified, the issues of the documents which are DoD adopted are those listed in the issue of the DoDISS cited in the solicitation. Unless otherwise specified, the issues of these documents are those cited in the solicitation or contract.
AMERICAN SOCIETY FOR QUALITY (ASQ)
Z1.4 – Sampling Procedures and Tables for Inspection by Attributes (DoD
adopted).
(Application for copies should be addressed to the American Society for Quality, P.O. Box 3005, Milwaukee, WI 53201-3005 or at http://www.asq.org).
ASTM INTERNATIONAL
D 56 – Standard Test Method for Flash Point by Tag Closed Cup Tester
D 86 – Standard Test Method for Distillation of Petroleum Products at Atmospheric
Pressure
D 130 – Standard Test Method for Corrosiveness to Copper from Petroleum
Products by Copper Strip Test
D 156 – Standard Test Method for Saybolt Color of Petroleum Products (Saybolt
Chromometer Method)
D 235 – Standard Test Method for Mineral Spirits (Petroleum Spirits) (Hydrocarbon
Dry-Cleaning Solvent)
D 847 – Standard Test Method for Acidity of Benzene, Toluene, Xylenes, Solvent
Naphthas, and Similar Industrial Aromatic Hydrocarbons
D 1133 – Standard Test Method for Kauri-Butanol Value of Hydrocarbon Solvents
D 1296 – Standard Test Method for Odor of Volatile Solvents and Diluents
D 1298 – Standard Test Method for Density, Relative Density (Specific Gravity), or
API Gravity of Crude Petroleum and Liquid Petroleum Products by
Hydrometer Method
D 1353 – Standard Test Method for Nonvolatile Matter in Volatile Solvents for Use in
Paint, Varnish, Lacquer, and Related Products
D 2879 – Standard Test Method for Vapor Pressure-Temperature Relationship and
Initial Decomposition Temperature of Liquids by Isoteniscope
D 3257 – Standard Test Method for Aromatics in Mineral Spirits by Gas
Chromatography
D 4057 – Standard Practice for Manual Sampling of Petroleum and Petroleum
Products
D 4177 – Standard Practice for Automatic Sampling of Petroleum and Petroleum
Products
F 483 – Standard Test Method for Total Immersion Corrosion Test for Aircraft
Maintenance Chemicals
F 945 – Standard Test Method for Stress-Corrosion of Titanium Alloys by Aircraft
Engine Cleaning Materials
F 1110 – Standard Test Method for Sandwich Corrosion Test
(Application for copies should be addressed to ASTM International, 100 Barr Harbor Drive, West Conshohocken, PA 19428-2959 or at http://www.astm.org).
SOCIETY OF AUTOMOTIVE ENGINEERS (SAE)
AMS-QQ-A-250 – Aluminum and Aluminum Alloy, Plate and Sheet (DoD
adopted).
AMS 2470 – Anodic Treatment of Aluminum Alloys Chrome Acid Process
(DoD adopted).
AMS M 3171 – Magnesium Alloy, Processes for Pretreatment and Prevention
of Corrosion on (DoD adopted).
AMS 4377 – Magnesium Alloy, Sheet and Plate 3.0A1-1.0Zn-0.20Mn
(AZ31B-H24) Cold Rolled, Partially Annealed
AMS 4911 – Titanium Alloy Sheet, Strip, and Plate, 6AI-4V Annealed
AMS 5046 – Carbon Steel Sheet, Strip, and Plate, (SAE 1020 and 1025)
Annealed
(Application for copies should be addressed to the Society of Automotive Engineers, Inc., 400 Commonwealth Drive, Warrendale, PA 15096-0001 or at http://www.sae.org).
2.4 Order of precedence. In the event of a conflict between the text of this specification and the references cited herein, the text of this specification takes precedence. Nothing in this specification, however, supersedes applicable laws and regulations unless a specific exemption has been obtained.
3. REQUIREMENTS
3.1 Qualification. Solvents furnished under this specification shall be products that are authorized by the qualifying activity for listing on applicable qualified products list before contract award (see 4.2 and 6.3). Any change in the formulation of a qualified product will necessitate its requalification.
3.2 Materials. The hydrocarbon solvent shall be a virgin grade or recycled solvent derived from petroleum distillates, fraction from reclaiming and re-refining processes, or a mixture of these fractions. The d-limonene and hydrocarbon blended solvent is permitted as a Type IV solvent. The EPA exempt materials and hydrocarbon blended solvent is also permitted as a Type V solvent. The resultant solvent must be produced in such a manner as is necessary to meet the specified requirements.
3.3 Appearance. The solvent shall be clear and free from suspended matter and undissolved water when observed at a temperature between 60.1 and 78.1°F (15.6 and 25.6 °C).
3.4 Toxicity. The solvent shall have no adverse effects on human health when used as intended (see 6.1 and 6.6).
3.5 Carcinogenicity. The solvent shall contain no chemicals listed as carcinogens (see 6.7). Any carcinogenic components in the solvent in a concentration of 0.1 percent (%) or greater by weight (wt) or volume (vol) will be regarded as the presence of a carcinogen in the solvent.
3.6 Hazardous Air Pollutants. The solvent shall contain no chemicals listed as Hazardous Air Pollutants (HAPs) (see 6.7). Any HAP components in the solvent in a concentration of 1.0 percent (%) or greater by weight (wt) or volume (vol) will be regarded as the presence of a HAP in the solvent. The product containing less than 1 % of HAP shall be considered as a HAP free solvent. For carcinogenic HAPs see 3.5.
3.7 Physical and chemical property requirements. The solvents shall conform to the physical and chemical requirements in Table I when tested as specified in Table II.
TABLE I. Degreasing solvent properties.
1/ Samples of MIL-PRF-680C, Type III, having satisfactory low odor characteristics
shall be used as reference standards.
2/ Test for three hours at 100 °C (212oF).
3/ See 4.4.2
4/ Not required
4. VERIFICATION
4.1 Classification of inspections. The inspection requirements specified herein are
classified as follows:
a. Qualification inspection (see 4.2)
b. Conformance inspection (see 4.3).
4.1.1 Inspection conditions. Unless otherwise specified, all inspections shall be performed in accordance the test conditions specified in 4.2.
4.2 Qualification inspection. The qualification inspection shall consist of all tests specified herein. Failure of any test shall be cause for rejection.
4.3 Conformance inspection. Conformance inspection shall consist of a sample for tests (see 4.3.2), samples for examination of filled containers (see 4.3.3), and the tests specified in Table II except for sandwich corrosion, total immersion corrosion, and titanium stress corrosion.
4.3.1 Lot. A lot shall consist of solvents from one batch or tank offered for delivery at one time. If material cannot be identified by batch or lot, a lot shall consist of not more than 10 000 gallons offered for delivery at one time (see 6.2).
4.3.2 Sampling for tests. Sampling of a lot for test purposes shall be in accordance with ASTM D 4057 or D 4177.
4.3.3 Sample for examination of filled containers. A random sample of filled unit containers and a sample of shipping containers fully prepared for delivery shall be selected from each lot of solvent in accordance with ASQ Z1.4.
4.4 Methods of inspection.
4.4.1 Tests. Tests shall be performed in accordance with the applicable methods specified in Table II and 4.4.2 through 4.4.3 to determine conformance with the requirements specified in 3.6.
TABLE II. Test methods for inspections.
4.4.2 Total immersion corrosion. The solvents shall not show any indication of staining, etching, pitting, or localized, or cause weight change to an average of three (3) test panels greater than that shown in Table III.
TABLE III. Alloy and maximum average weight loss.
4.4.3 Soil cleaning test. The test shall be conducted according to the solvent soil test method described in the appendix. The soil used in this evaluation is MIL-PRF-10924 grease. The acceptable limit for each type of solvent is defined in Table I.
4.4.4 Total chlorine content. The total chlorine content of the solvent shall be determined by a gas chromatographic method, microcoulometric or by the use of a portable test kit for the quantitative analysis of chlorine (see 6.6). Nonconformance to Table I shall constitute failure of this test.
5. PACKAGING
5.1 Packaging. For acquisition purpose, the packaging requirements shall be as specified in the contract or order (see 6.2). When actual packaging of materiel is to be performed by DoD personnel, these personnel need to contact the responsible packaging activity to ascertain requisite packaging requirements. Packaging requirements are maintained by the Inventory Control Point’s packaging activity with the Military Department or Defense Agency, or within the Military Department’s System Command. Packaging data retrieval is available from the managing Military Department’s or Defense Agency’s automated packaging files, CD-ROM products, or by contracting the responsible packaging activity.
6. NOTES
(This section contains information of a general or explanatory nature that may be helpful, but is not mandatory.)
6.1 Intended use. These solvents are hydrocarbon-based solvents and are used as degreasers and cleaners for painted or unpainted metal parts. However, the compatibility between existing paints and solvents should be verified prior to use. It is recommended that these solvents should be used with an appropriate recirculated parts washer. No other commercial specification is available to cover these military applications.
6.1.1 Type I. Type I (Stoddard solvent) is intended for use where a low odor solvent with fast drying characteristics is desired. This solvent is currently defined as a flammable material due to its low flash point. It is recommended that the alternative solvents for Type I are Types II, III and IV. When Type I solvent is used indoors, ventilation should be sufficient to prevent the accumulation of vapors above allowable limits.
6.1.2 Type II. Type II (low odor with high flash point solvent) is intended for use where a solvent with a higher flash point is desired. It is recommended over Type I for safety and regulatory reasons. When Type II solvent is used indoors, ventilation should be sufficient to prevent the accumulation of vapors above allowable exposure limits.
6.1.3 Type III. Type III (low odor with very high flash point solvent) is intended to be used where confined atmospheric conditions require a cleaner that conforms to the Federal Government’s directives for reduced hazardous materials.
6.1.4 Type IV. Type IV (citrus odor with high flash point) is intended for use where a solvent with a high flash point and strong solvency is desired. This solvent is formulated with petroleum based hydrocarbon solvents and d-limonene additive. When Type IV solvent is used indoors, ventilation should be sufficient to prevent the accumulation of vapors above allowable exposure limits.
6.1.5 Type V. Type V (Low VOC solvent) is intended for use where solvent confined atmospheric conditions require a cleaner that conforms to the Federal and Local Government’s directives for reducing VOC of solvent.
6.2 Acquisition requirements. Acquisition documents must specify the following:
a. Title, number and date of this specification.
b. Type and quantity (see 1.2. and 4.3.1).
c. Issue of DODISS to be cited in the solicitation, and if required, the specific issue of individual documents referenced (see 2.2.1 and 2.3).
d. Packaging requirements (see 5.1)
6.3 Qualification. With respect to products requiring qualification, awards will be made only for products which are at the time of award of contract, qualified for inclusion in Qualified Product List QPL No. 680 whether or not such products have actually been so listed by that date. The attention of the contractors is called to these requirements, and manufacturers are urged to arrange to have the products that they propose to offer to the Federal Government tested for qualification in order that they may be eligible to be awarded contracts or purchase orders for the products covered by this specification.
6.3.1 Specification preparing activity. Information and instructions regarding qualification inspection under this specification may be obtained from the Department of the Army, TACOM-TARDEC, ATTN: AMSRD-TAR-E/268, 6501 E. 11 Mile Road, Warren, MI 48397-5000.
6.4 International standardization. Certain provisions of this specification are the subject of international standardization agreement (NATO STANAG 1135, ANNEX C). When amendment, revision, or cancellation of this specification is proposed which would affect or violate the international agreement concerned, the preparing activity will take appropriate reconciliation action through international channels, including departmental standardization offices, if required.
6.5 Disposal actions. Disposal of this product should be in accordance with local, state and Federal regulations. Care should be taken to avoid mixing used MIL-PRF-680 with other waste materials, especially those containing halogenated solvents. However, these solvents can be recycled instead of disposal.
6.6 Material Safety Data Sheets. Contracting officers will identify those activities requiring copies of completed Material Safety Data Sheets (MSDSs) prepared in accordance with FED-STD-313. The pertinent Government mailing addresses for submission of data are listed in FED-STD-313; and 29 CFR 1910.1200 requires that the MSDS for each hazardous chemical used in an operation must be readily available to personnel using the material. Contracting officers will identify the activities requiring copies of the MSDS (see 3.4 and 4.4.4).
6.7 Definitions.
6.7.1 Carcinogens. The Occupational Safety and Health Administration (OSHA) definition of carcinogens are those chemicals / processes appearing in lists 1, 2A, and 2B of the International Agency for Research on Cancer (IARC) 1/; substances known to be carcinogenic and occupational exposures associated with a technological process known to be carcinogenic by the National Toxicology Program (NTP) Report on Carcinogens (latest annual report) 2/; and OSHA regulated carcinogens.
6.7.2. Hazardous Air Pollutant (HAP). HAP is defined as any substance listed under Section 112 of the Clean Air Act or its modifications. The text of the Clean Air Act, listed pollutants and modifications are kept by the Environmental Protection Agency (EPA) and are accessible through the website: http://www.epa.gov
1/ Copies of these volumes may be found in medical libraries or through the World Health Organization, 1211 Geneva 27, Switzerland.
2/ Copies may be obtained from the Public Health Service, National Toxicology Program, Public Information Office, P.O. Box 12233, MD B2-04, Research Triangle Park, NC 27709 or at http://ntp-server.niehs.nih.gov
6.8 Subject term (key word) listing.
d-limonene
d-limonene/hydrocarbon blended solvent (type IV)
Mineral Spirits
Naphtha
Petroleum Spirits (USA)
Stoddard Solvent (type I)
141 F Solvent (type II)
200 F Solvent (type III)
Low VOC Solvent (type V)
6.9 Changes from previous issues. Marginal notations are not used in this revision to identify changes with respect to the previous issue due to the extensiveness of the changes.
Custodians: Army – AT Preparing Activity:
Air Force – 68 Navy – AS Army – AT
(Project 6850-2010-007)
Review Activities:
Army – AV, EA, MD1, MI, MR, SM
Air Force – 03, 11, 50
Navy – MC, SH
DLA – GS, GS3, DP
DTRA – DS
GSA/GSS – 7FLE
MISC – MP
NOTE: The activities listed above were interested in this document as of the date of this document.
MIL PRF 680C Type V Replaces MIL PRF 680B Type II
/in Ecolink News/by Industrial DegreasersMIL PRF 680C Type V Replaces MIL PRF 680B Type II
Ecolink Inc is pleased to announce their exclusive distinction as the only approved alternative to MIL PRF 680B Type II. MIL PRF 680C Type V is a low VOC alternative that complies with the most stringent air emission standards and will be sold under the trade name of Ecolink 250-SS.
MIL PRF 680 Type II Cannot be Used in the Following Areas:
MIL PRF 680 C – Type V – to download a PDF copy
Contec Wipes, Contec Wipers & Contec Prosat Available from Ecolink
/in Ecolink News/by Industrial DegreasersDo you buy Contec Wipers, Contec Wipes, or Contec Prosat?
Save time & money with Ecolink Inc. – Mention “April Blog” for special pricing
Ecolink Inc. – #1 Contec Cleanroom Distributor
For over 15 years, Ecolink Inc. ranks as a top tier Contec cleanroom distributor of Contec Wipers, Contec Wipes, and Contec Prosat. We value our long-standing supply agreements with Lockheed Martin and Pratt & Whitney and eager to expand the number of Contec customers we can save $ and time. Unlike other wipe, wiper and cleanroom distributors, we deliver multiple products and services so you have fewer calls, emails to make and take; dramatically reduce accounting burden with different PO’s, payment terms, financial accounting systems; save $ on the product and delivery costs.
Contec Wipers – available at www.ecolink.com
Contec Wipes – available at www.ecolink.com
Contec PROSAT – available at www.ecolink.com
Genesolv HCFC 141b – Replacement Options for Cleaning Gauges
/in Ecolink News/by Industrial DegreasersHCFC 141b is still available!
HCFC 141b is SCAQMD compliant and works especially well for cleaning non-oxygen system gauges used in lubricating and hydraulic service such as on submarines. A common method to clean these types of gauges involves a piece of equipment specifically designed to clean gauges with a liquid solvent and then remove the residual solvent using a vacuum pump. The solvent is pumped into the gauge and circulated. The residual liquid is then removed using a vacuum pump. The vacuum removal process lowers the pressure inside the gauge enough to make the solvent liquid vaporize and be removed as a gas. The machine then collects the spent liquid solvent in a container. 3M’s HFE-71DE, NSN 6850-01-459-0069 is also approved for this type of cleaning application. If you are not fully satisfied with cleaning performance, cost, service, etc. for sourcing and cleaning with HFE-71DE, please call or email us to discuss your technical requirements and where HCFC 141b can satisfy your critical cleaning needs.
HCFC 141b is ‘the’ solvent where the following conditions are mission critical:
Attention all users of Honeywell Genesolv® SF, Genesolv® S-TZ & Genesolv® S-T
Please call 800 886-8240 or email info@ecolink.com to discuss cost effective alternatives. The Genesolve S series are very costly materials and ‘may’ be used in less than critical cleaning applications. As HCFC 141b supplies continue to dwindle the list of alternatives continue to expand. There is no one size fits all that meets cleaning performance, environmental/health/safety and cost-benefit criteria. Whether you are in a bulk or aerosol cleaning application, we strongly recommend matching the value of the cleaner to the value of the part, equipment, and/or labor.
NMP Solvent – Acetone Replacement for Fiberglass Tools and Spray Guns
/in Ecolink News, NMP Solvent/by Industrial DegreasersNMP Solvent – 3 reasons to replace acetone for cleaning fiberglass tools and spray guns
Attention all fiberglass boat builders (SIC Code: 3732), and boat repair (SIC Code: 449304) NOW is the time to stop using acetone in the cleaning operation for fiberglassing tools and spray guns.
By switching to Safe Strip, an NMP (N-methyl pyrollidone) based solvent with a flashpoint of 201 degrees Fahrenheit for general cleaning and gun flushing. Safe Strip, same as most NMP-based solvents, is recycled via commercial recycling equipment or by recycling service providers who conduct distillation on-site. Very little Safe Strip is lost due to volatilization, and companies can expect an estimated 90% recovery rate.