Making the switch to environmentally preferred solvents is a great way to protect the environment and your team’s health. But with an array of...
Blog
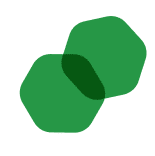
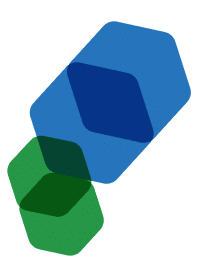
CHEMICAL INDUSTRY NEWS
Chemical Chat – Discover What’s New!
What Are the Best Eco-Preferred Industrial Degreasers Available?
Choosing the right eco-friendly degreaser for your business can be tough—from finding suppliers to combing through page after page of products, it’s...
Chemical Solvent Suppliers: Why Businesses Choose Ecolink!
Looking for new chemical solvent suppliers? You’re not alone. Considering that just about every industry requires chemicals, having a chemical...
What are the top environmentally safe solvent options with Ecolink?
Making the switch to environmentally preferred solvents is a great way to protect the environment and your team’s...
What Are the Best Eco-Preferred Industrial Degreasers Available?
Choosing the right eco-friendly degreaser for your business can be tough—from finding suppliers to combing through...
Company News
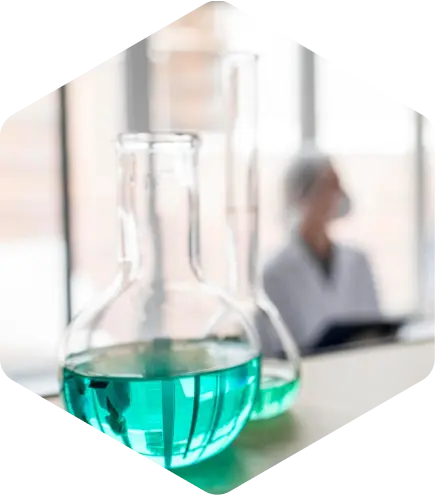
Managed Services
Discover the Latest in Safe and Sustainable Chemical Solutions
Stay informed with Ecolink’s blog! Subscribe now
Chemical Management Information
Stay updated with us
Sign Up for the Latest Updates
Stay informed about chemical supply chain disruptions and emerging innovations to keep your business at the forefront of efficiency and innovation. Uncover new ways to make your business practices more sustainable by incorporating safer products into your cleaning lineup.