It seems like almost anything can be recycled these days: tires, gasoline, motor oil, cotton fibers, degreaser, and the list goes on. If there’s one item in the list that many people don’t think of as recyclable, it’s degreaser, much less a specific class of...
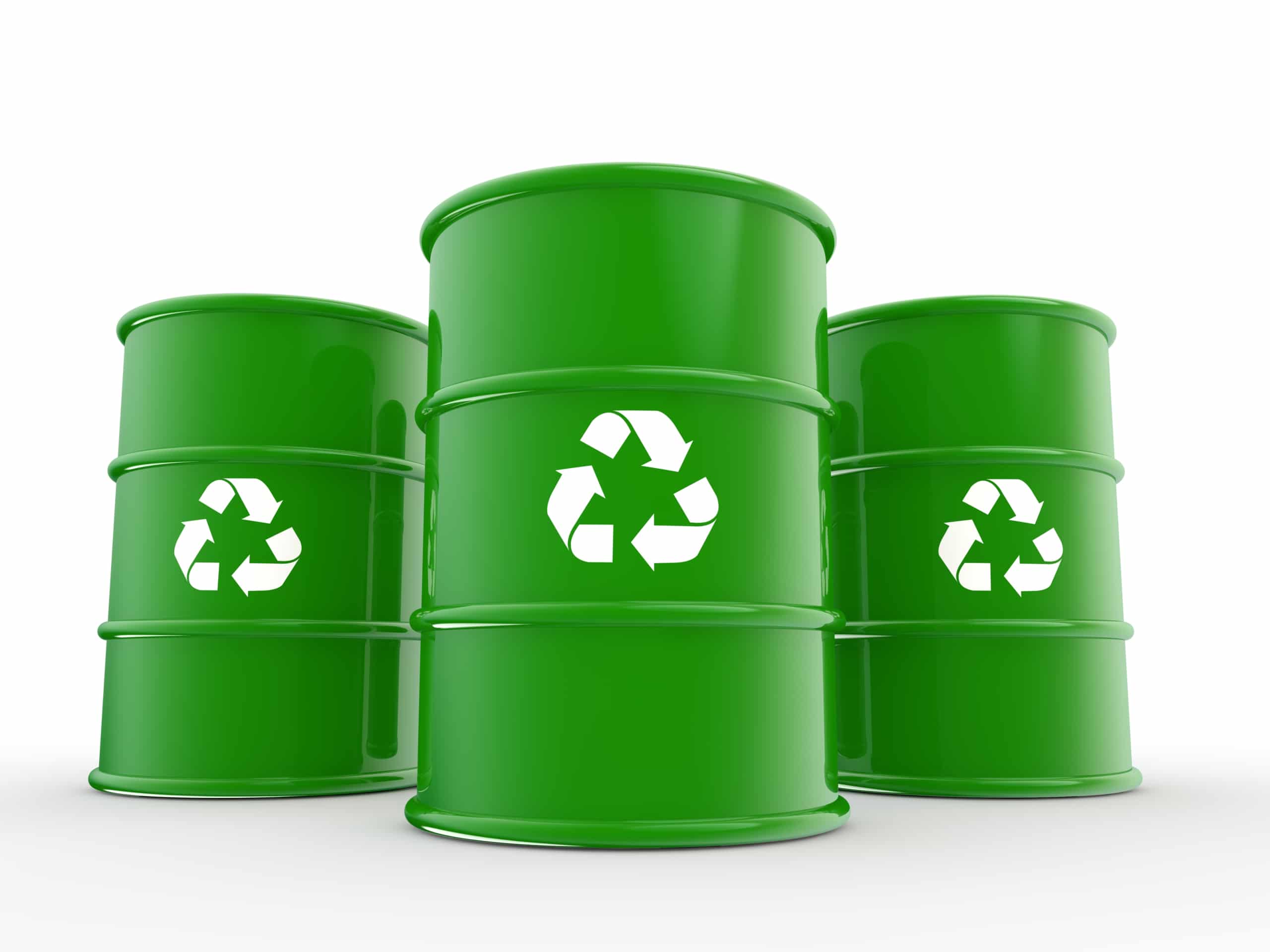