Contact cleaner is formulated to clean the electrical contacts in equipment and devices that complete the electrical circuits they contain. In most cases, companies and organizations choose to apply contact cleaner in one of three forms: aerosol, liquid, or wipes....
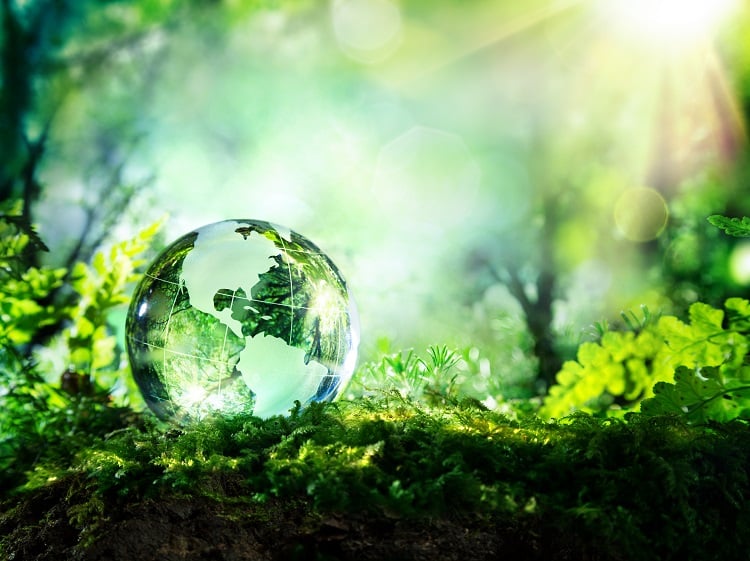