[av_gallery ids='14388' style='big_thumb lightbox_gallery' preview_size='large' crop_big_preview_thumbnail='avia-gallery-big-crop-thumb' thumb_size='portfolio' columns='5' imagelink='lightbox' lazyload='avia_lazyload' av_uid='av-jx4q2a7i' admin_preview_bg=''] [av_hr...
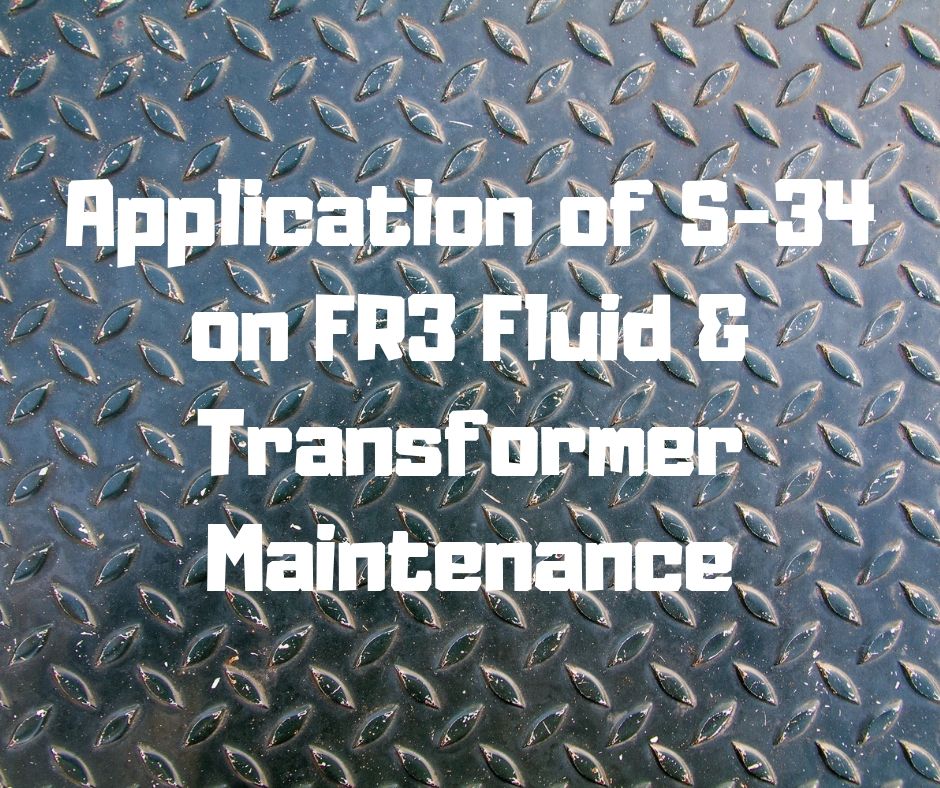