Solvents are substances utilized by multiple industries for diverse applications. Non-chlorinated and chlorinated solvents are two examples among...
Blog
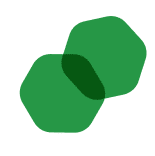
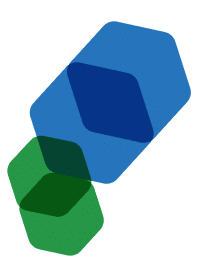
CHEMICAL INDUSTRY NEWS
Chemical Chat – Discover What’s New!
Resin Solvent Spray: Cleaning and Maintenance Solution
From artists crafting their masterpieces to engineers using 3D printers, many industries utilize resin. However, this could become a problem when...
Exploring Algaecide Chemicals for Effective Treatment
No matter the products that they produce or how many consumers they provide for, every industry utilizes water for its industrial applications. This...
Resin Remover Spray: Efficient Cleaning Solution for Industrial Use
Resin can be both naturally occurring and synthetically made. It is a viscous substance: when cured, it becomes a...
Resin Solvent Spray: Cleaning and Maintenance Solution
From artists crafting their masterpieces to engineers using 3D printers, many industries utilize resin. However, this...
Company News
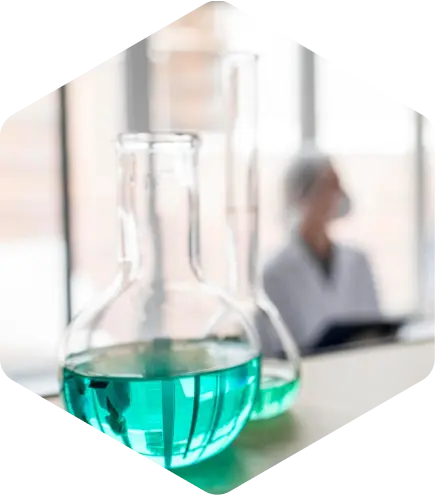
Managed Services
Discover the Latest in Safe and Sustainable Chemical Solutions
Stay informed with Ecolink’s blog! Subscribe now
Chemical Management Information
Stay updated with us
Sign Up for the Latest Updates
Stay informed about chemical supply chain disruptions and emerging innovations to keep your business at the forefront of efficiency and innovation. Uncover new ways to make your business practices more sustainable by incorporating safer products into your cleaning lineup.