Most resin and coating removers are very strong solvents, as they need to be able to effectively penetrate the layers of paints and resins to loosen...
Blog
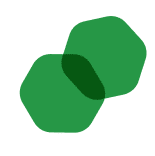
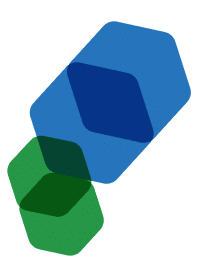
CHEMICAL INDUSTRY NEWS
Chemical Chat – Discover What’s New!
The Benefits of Tidal Brown Soap
Are You Interested in an Industrial Truck Wash? Have you been looking for a new industrial truck wash solution? Tidal Brown Soap might just be the...
The Benefits of Tidal Bleach Neutralizer
What Is Tidal Bleach Neutralizer? Tidal Bleach Neutralizer is an alkaline solution whose main ingredient is sodium hyposulfite (10%-20% by...
The Benefits of Tidal Citrus Cleaner
Looking for a New House Exterior Cleaner? If so, you’re in luck! Tidal Citrus Cleaner is an industrial-strength...
The Benefits of Tidal Brown Soap
Are You Interested in an Industrial Truck Wash? Have you been looking for a new industrial truck wash solution?...
Company News
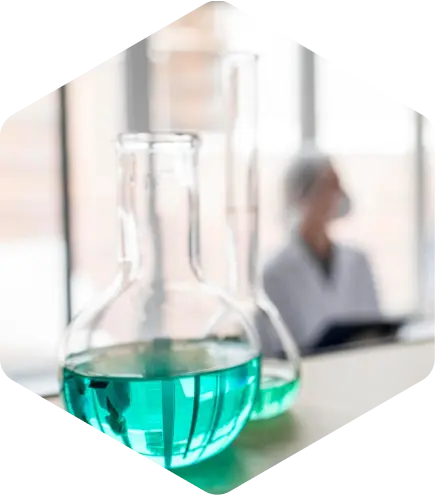
Managed Services
Discover the Latest in Safe and Sustainable Chemical Solutions
Stay informed with Ecolink’s blog! Subscribe now
Chemical Management Information
Stay updated with us
Sign Up for the Latest Updates
Stay informed about chemical supply chain disruptions and emerging innovations to keep your business at the forefront of efficiency and innovation. Uncover new ways to make your business practices more sustainable by incorporating safer products into your cleaning lineup.