One of the biggest problems that water cooling systems can face is corrosion, which occurs when water interacts with the metals in the structure and...
Blog
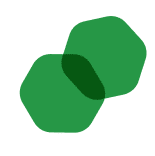
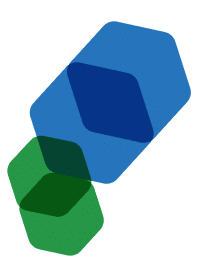
CHEMICAL INDUSTRY NEWS
Chemical Chat – Discover What’s New!
Is Turpentine The Same As Mineral Spirits
Is turpentine the same as mineral spirits? No, it is not. While turpentine and mineral spirits may share some similar applications they are...
Difference Between Acetone And Acetate
What is the difference between acetone and acetate? To adequately explain the differences between acetone and acetate, it is important to define...
Getting to Know Naomi Davis
Naomi Davis is a student at the University of Central Florida, studying social work. She is one of Ecolink’s six $500...
Is Turpentine The Same As Mineral Spirits
Is turpentine the same as mineral spirits? No, it is not. While turpentine and mineral spirits may share some similar...
Company News
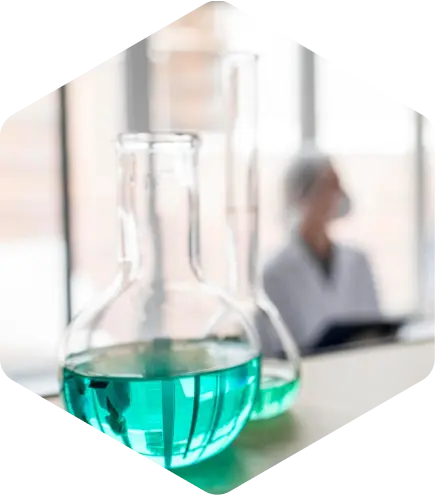
Managed Services
Discover the Latest in Safe and Sustainable Chemical Solutions
Stay informed with Ecolink’s blog! Subscribe now
Chemical Management Information
Stay updated with us
Sign Up for the Latest Updates
Stay informed about chemical supply chain disruptions and emerging innovations to keep your business at the forefront of efficiency and innovation. Uncover new ways to make your business practices more sustainable by incorporating safer products into your cleaning lineup.