Water is used often as a cheap, plentiful, and effective coolant in industrial settings. However, pumping large quantities through commercial...
Blog
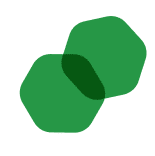
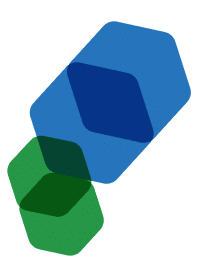
CHEMICAL INDUSTRY NEWS
Chemical Chat – Discover What’s New!
N Heptane Uses
N heptane uses are vast. Besides being considered a great solvent, n heptane uses include it being a standard-bearer in the testing of the knock...
What Are Naptha Solvents Used For?
What are naptha solvents used for? Typically naptha solvents are used in cleaning liquids to break down hard oils, especially when other solvents...
Where To Buy Heptane
Wondering where to buy heptane in bulk? Ecolink is a trusted, industrial supplier of many chemicals, including...
N Heptane Uses
N heptane uses are vast. Besides being considered a great solvent, n heptane uses include it being a standard-bearer...
Company News
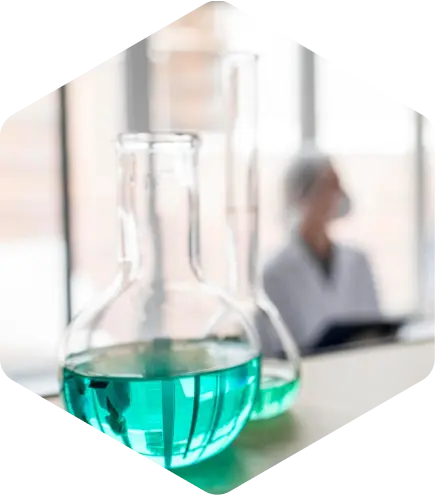
Managed Services
Discover the Latest in Safe and Sustainable Chemical Solutions
Stay informed with Ecolink’s blog! Subscribe now
Chemical Management Information
Stay updated with us
Sign Up for the Latest Updates
Stay informed about chemical supply chain disruptions and emerging innovations to keep your business at the forefront of efficiency and innovation. Uncover new ways to make your business practices more sustainable by incorporating safer products into your cleaning lineup.