MEK, also known as methyl ethyl ketone, is a familiar chemical to many industries, as it is relied on for a wide range of processes, such as ...
Blog
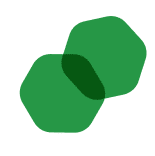
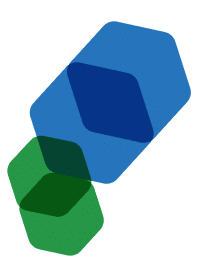
CHEMICAL INDUSTRY NEWS
Chemical Chat – Discover What’s New!
The Chemical Industry & Supply Chain Disruptions
In everyday life, it’s common to not be able to get the products and supplies a consumer needs due to the many supply chain disruptions our world is...
The Benefits of Green Concrete Remover
Definition of Green Concrete Remover Do you work in an industry that frequently uses concrete? If so, you know how difficult it is to remove...
The Benefits of Industrial Metal Prep
What Is Industrial Metal Prep? Industrial Metal Prep is a commercial cleaning solution that is primarily made up of...
The Chemical Industry & Supply Chain Disruptions
In everyday life, it’s common to not be able to get the products and supplies a consumer needs due to the many supply...
Company News
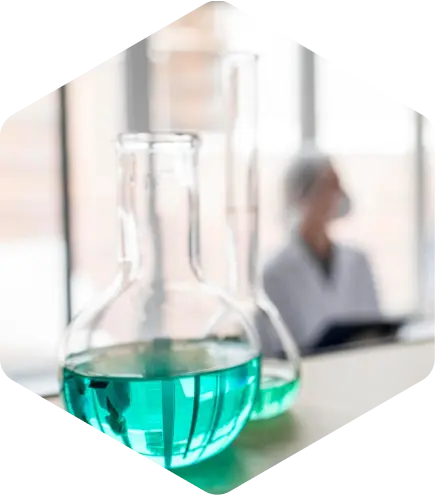
Managed Services
Discover the Latest in Safe and Sustainable Chemical Solutions
Stay informed with Ecolink’s blog! Subscribe now
Chemical Management Information
Stay updated with us
Sign Up for the Latest Updates
Stay informed about chemical supply chain disruptions and emerging innovations to keep your business at the forefront of efficiency and innovation. Uncover new ways to make your business practices more sustainable by incorporating safer products into your cleaning lineup.