As environmental concerns continue to grow, businesses are recognizing the importance of using ecofriendly fuel. Traditional fossil fuels have long...
Blog
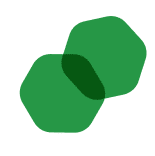
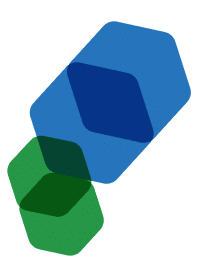
CHEMICAL INDUSTRY NEWS
Chemical Chat – Discover What’s New!
Low Global Warming Potential Solvents: A Sustainable Alternative for Industrial Cleaning
As minimizing global warming becomes a greater and greater priority, efforts toward reducing contributions are at an all-time high. The chemical...
Azeotrope-like Solvents: The Next Generation of Industrial Cleaning Solutions
A recent trend in the chemical industry is that of taking advantage of azeotropes. These unique mixtures have special properties that can be of...
Industrial Cooling Water Systems: Overview and Applications
An industrial cooling water system is a cost-effective way to remove heat from processes and process equipment....
Low Global Warming Potential Solvents: A Sustainable Alternative for Industrial Cleaning
As minimizing global warming becomes a greater and greater priority, efforts toward reducing contributions are at an...
Company News
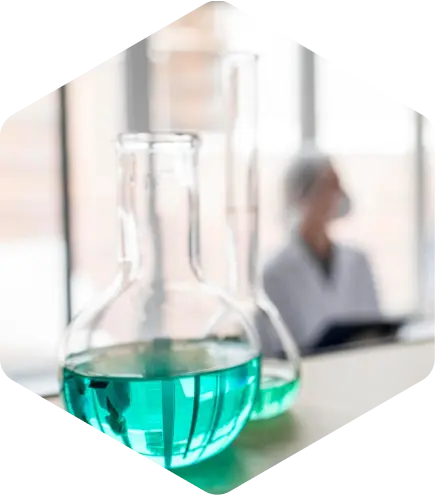
Managed Services
Discover the Latest in Safe and Sustainable Chemical Solutions
Stay informed with Ecolink’s blog! Subscribe now
Chemical Management Information
Stay updated with us
Sign Up for the Latest Updates
Stay informed about chemical supply chain disruptions and emerging innovations to keep your business at the forefront of efficiency and innovation. Uncover new ways to make your business practices more sustainable by incorporating safer products into your cleaning lineup.