When I saw Ecolink posted as an Internship opportunity on LinkedIn I knew I had to apply. While I have several internships under my belt, I was...
Blog
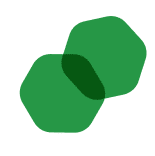
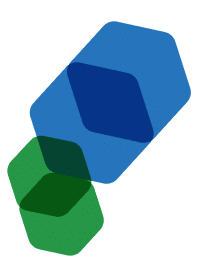
CHEMICAL INDUSTRY NEWS
Chemical Chat – Discover What’s New!
Hannah’s Internship Experience
By Hannah Frisch 2020, A year we’ve all found our struggles in. Being a college student and heading towards my final semester in college before...
Can You Use Hexane For Oil Extraction?
If you work in an industry that extracts oils from plant materials, you may want to look into hexane for oil extraction. Oil extraction is a process...
Mohammed’s Internship Experience
Clicking that link and filling out that form was nerve-wracking; it’s scary thinking you’re unqualified or not good...
Hannah’s Internship Experience
By Hannah Frisch 2020, A year we’ve all found our struggles in. Being a college student and heading towards my final...
Company News
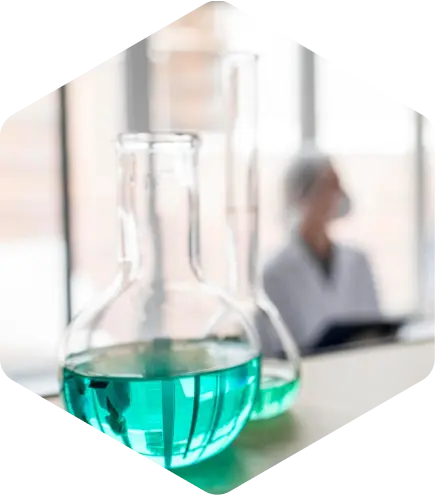
Managed Services
Discover the Latest in Safe and Sustainable Chemical Solutions
Stay informed with Ecolink’s blog! Subscribe now
Chemical Management Information
Stay updated with us
Sign Up for the Latest Updates
Stay informed about chemical supply chain disruptions and emerging innovations to keep your business at the forefront of efficiency and innovation. Uncover new ways to make your business practices more sustainable by incorporating safer products into your cleaning lineup.