Algae is a simple plant and only needs a few things to prosper: water, sunlight, and nutrients like carbon, nitrogen, and phosphorus. This simple...
Blog
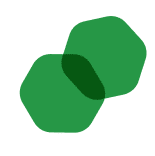
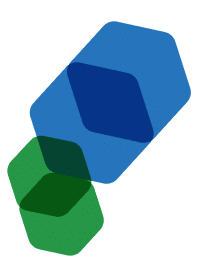
CHEMICAL INDUSTRY NEWS
Chemical Chat – Discover What’s New!
Anti Foaming Agents – What are they and why do they matter?
Understanding what anti foaming agents are and how they differ from de-foaming agents is the first step in deciding which kind of product might suit...
The Benefits of Chloriclean
Looking for a New Cleaning Solution? Do you work in the food manufacturing or processing industry? If so, you know how imperative it is to use a...
Types of Anti foaming Agents
What Are the different types of anti foaming agents and what are they used for? Popular perceptions of anti foaming...
Anti Foaming Agents – What are they and why do they matter?
Understanding what anti foaming agents are and how they differ from de-foaming agents is the first step in deciding...
Company News
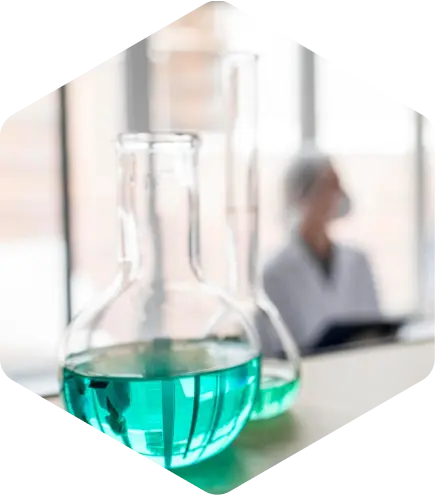
Managed Services
Discover the Latest in Safe and Sustainable Chemical Solutions
Stay informed with Ecolink’s blog! Subscribe now
Chemical Management Information
Stay updated with us
Sign Up for the Latest Updates
Stay informed about chemical supply chain disruptions and emerging innovations to keep your business at the forefront of efficiency and innovation. Uncover new ways to make your business practices more sustainable by incorporating safer products into your cleaning lineup.