Most people know that a product labeled as biodegradable is considered an eco-friendly option, but not many know what the term actually means, or...
Blog
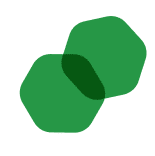
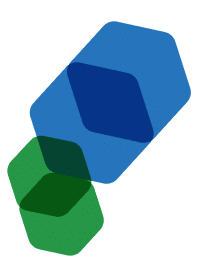
CHEMICAL INDUSTRY NEWS
Chemical Chat – Discover What’s New!
Why Is Chemical Treatment of Cooling Towers Needed?
Why is chemical treatment of cooling towers needed? The primary objective of a cooling tower is to maintain healthy working conditions in your...
Cooling Tower Water Chemicals
Why are cooling tower water chemicals needed? The primary objective of a cooling tower is to maintain healthy working conditions in your buildings....
Discover Cooling Tower Chemicals for Your System!
To better understand cooling tower chemicals, it is important to understand the types of compounds and microorganisms...
Why Is Chemical Treatment of Cooling Towers Needed?
Why is chemical treatment of cooling towers needed? The primary objective of a cooling tower is to maintain healthy...
Company News
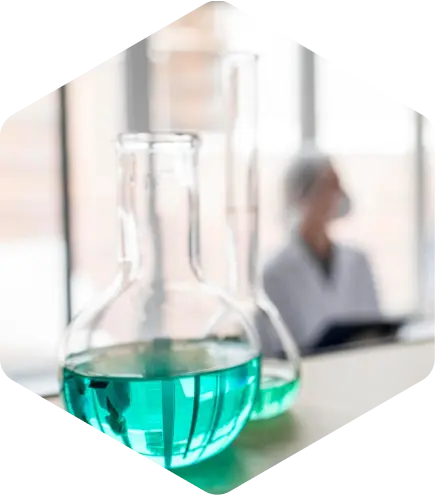
Managed Services
Discover the Latest in Safe and Sustainable Chemical Solutions
Stay informed with Ecolink’s blog! Subscribe now
Chemical Management Information
Stay updated with us
Sign Up for the Latest Updates
Stay informed about chemical supply chain disruptions and emerging innovations to keep your business at the forefront of efficiency and innovation. Uncover new ways to make your business practices more sustainable by incorporating safer products into your cleaning lineup.