Aggressive paint removers tend to have one specific chemical property that may be undesirable to certain individuals or companies: flammability. ...
Blog
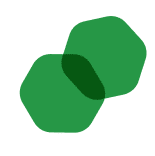
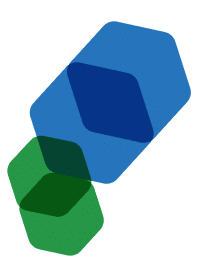
CHEMICAL INDUSTRY NEWS
Chemical Chat – Discover What’s New!
Is Sodium Hypochlorite The Same As Bleach?
Is sodium hypochlorite the same as bleach? The chemical term for bleach is sodium hypochlorite. Perhaps a brief history of bleach is an appropriate...
Discover Cooling Tower Chemicals for Your System!
To better understand cooling tower chemicals, it is important to understand the types of compounds and microorganisms and other buildups that...
Sodium Hypochlorite vs Chlorine
What is the difference between sodium hypochlorite vs chlorine? Sodium hypochlorite (the chemical name for bleach) is...
Is Sodium Hypochlorite The Same As Bleach?
Is sodium hypochlorite the same as bleach? The chemical term for bleach is sodium hypochlorite. Perhaps a brief...
Company News
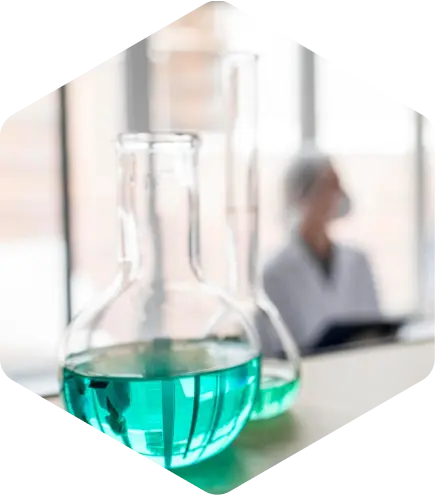
Managed Services
Discover the Latest in Safe and Sustainable Chemical Solutions
Stay informed with Ecolink’s blog! Subscribe now
Chemical Management Information
Stay updated with us
Sign Up for the Latest Updates
Stay informed about chemical supply chain disruptions and emerging innovations to keep your business at the forefront of efficiency and innovation. Uncover new ways to make your business practices more sustainable by incorporating safer products into your cleaning lineup.