The solvents in paint thinners dissolve the paint, making a thinner mixture that aids in the paint application process. While paint thinners are...
Blog
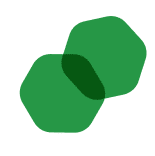
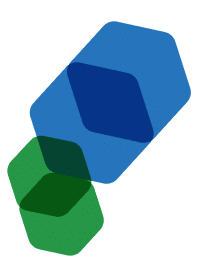
CHEMICAL INDUSTRY NEWS
Chemical Chat – Discover What’s New!
Sodium Hypochlorite For Soft Washing
Why is sodium hypochlorite for soft washing recommended? Sodium hypochlorite, (the chemical name for bleach) is commonly used as a disinfectant...
Best Soft Wash Chemicals
What are the best soft wash chemicals? Considering that generally, soft wash chemicals are known to only contain 3 primary ingredients, there are...
Sodium Hypochlorite House Wash Mix
Why use sodium hypochlorite house wash mix? Sodium hypochlorite (the chemical name for bleach) is an additive used in...
Sodium Hypochlorite For Soft Washing
Why is sodium hypochlorite for soft washing recommended? Sodium hypochlorite, (the chemical name for bleach) is...
Company News
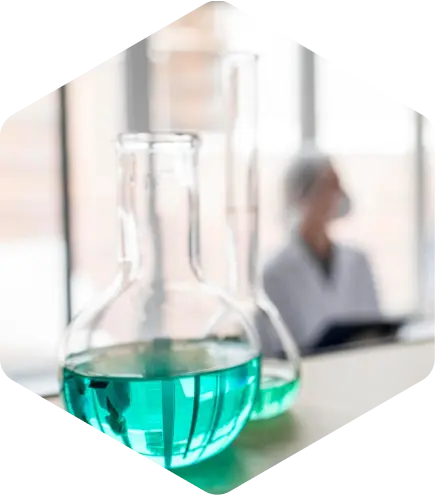
Managed Services
Discover the Latest in Safe and Sustainable Chemical Solutions
Stay informed with Ecolink’s blog! Subscribe now
Chemical Management Information
Stay updated with us
Sign Up for the Latest Updates
Stay informed about chemical supply chain disruptions and emerging innovations to keep your business at the forefront of efficiency and innovation. Uncover new ways to make your business practices more sustainable by incorporating safer products into your cleaning lineup.