MEK, also known as methyl ethyl ketone, is a controversial chemical that remains in the mainstream of various industries. The ketone industrial...
Blog
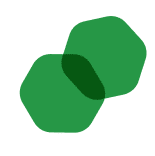
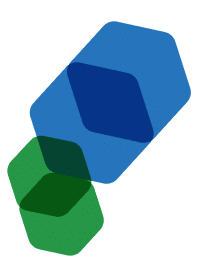
CHEMICAL INDUSTRY NEWS
Chemical Chat – Discover What’s New!
How do you test for Millipore?
How do you test for Millipore? The Millipore test standard is a process that requires a special setup of products designed to be operated together...
What is gravimetric cleanliness testing?
What is gravimetric cleanliness testing? The term gravimetric means to determine the weight of a particle and it's measurement. Gravimetric...
What chemical is used for Millipore?
What chemical is used for Millipore? Millipore is the name applied to the testing standard for gravimetrical analysis...
How do you test for Millipore?
How do you test for Millipore? The Millipore test standard is a process that requires a special setup of products...
Company News
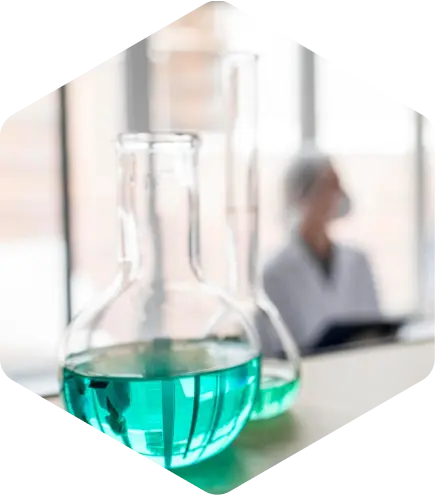
Managed Services
Discover the Latest in Safe and Sustainable Chemical Solutions
Stay informed with Ecolink’s blog! Subscribe now
Chemical Management Information
Stay updated with us
Sign Up for the Latest Updates
Stay informed about chemical supply chain disruptions and emerging innovations to keep your business at the forefront of efficiency and innovation. Uncover new ways to make your business practices more sustainable by incorporating safer products into your cleaning lineup.