Many companies and individuals rely on paint remover chemicals to strip paints/coatings and simultaneously clean a surface. For example, aircraft...
Blog
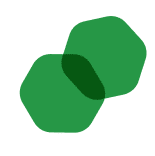
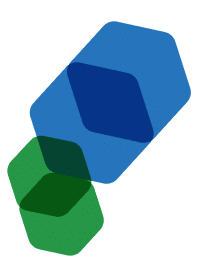
CHEMICAL INDUSTRY NEWS
Chemical Chat – Discover What’s New!
The Benefits of Red Fighter for Rust Stains
Looking for a Rust Stain Removal Product? No matter whether they’re on a vehicle, building, or some other kind of surface, rust stains can be...
The Benefits of Parts Metal Magic
Interested in a New Cleaning Powder for Your Spray Cabinet? If so, Parts Metal Magic might just be the product for you. Parts Metal Magic is a...
The Benefits of Red Super Tracker
Interested in a New Industrial Cleaning Solution? Red Super Tracker might just be the product for you. This red...
The Benefits of Red Fighter for Rust Stains
Looking for a Rust Stain Removal Product? No matter whether they’re on a vehicle, building, or some other kind of...
Company News
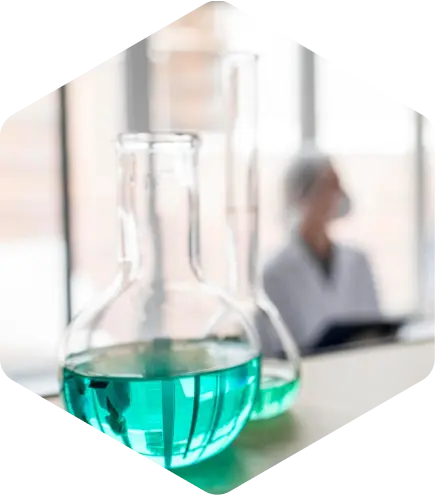
Managed Services
Discover the Latest in Safe and Sustainable Chemical Solutions
Stay informed with Ecolink’s blog! Subscribe now
Chemical Management Information
Stay updated with us
Sign Up for the Latest Updates
Stay informed about chemical supply chain disruptions and emerging innovations to keep your business at the forefront of efficiency and innovation. Uncover new ways to make your business practices more sustainable by incorporating safer products into your cleaning lineup.