If you have been in the market for multi-purpose green degreasers, Tidal SimpleClean is the perfect product for you. This alkaline solution,...
Blog
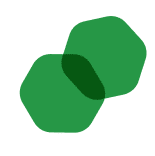
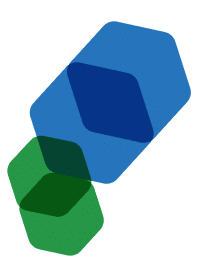
CHEMICAL INDUSTRY NEWS
Chemical Chat – Discover What’s New!
CA compliant IPA
What is CA compliant IPA? The state of california has certain requirements and restrictions that various chemicals and solvents must comply with....
Isopar L Suppliers
Choosing reliablable, and knowledgeable isopar L suppliers is important for many reasons. Isopar L is a versatile industrial solvent, and users...
Fracking Chemical Suppliers
What are common fracking chemicals and why is it important to work with reliable fracking chemical suppliers? Fracking...
CA compliant IPA
What is CA compliant IPA? The state of california has certain requirements and restrictions that various chemicals and...
Company News
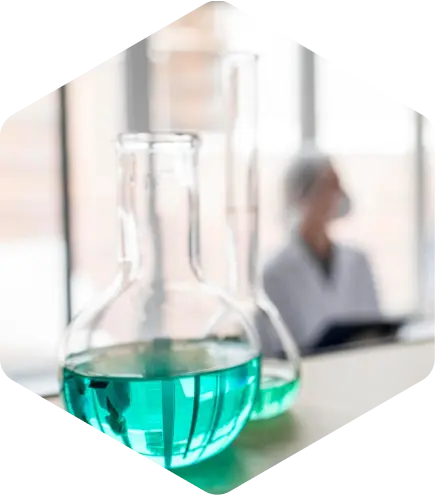
Managed Services
Discover the Latest in Safe and Sustainable Chemical Solutions
Stay informed with Ecolink’s blog! Subscribe now
Chemical Management Information
Stay updated with us
Sign Up for the Latest Updates
Stay informed about chemical supply chain disruptions and emerging innovations to keep your business at the forefront of efficiency and innovation. Uncover new ways to make your business practices more sustainable by incorporating safer products into your cleaning lineup.