The push for companies to use eco-friendly products has reached manufacturers of industrial cleaning solutions and the businesses that use them, as...
Blog
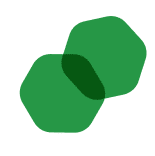
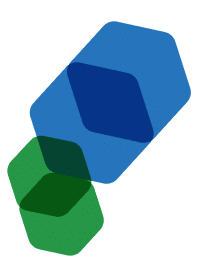
CHEMICAL INDUSTRY NEWS
Chemical Chat – Discover What’s New!
Reliable Acetone Manufacturers
Are you looking for reliable acetone manufacturers who can supply you with high quality chemicals and expert knowledge? Ecolink is a trusted...
Denatured Ethanol For Extraction
Is it safe to use denatured ethanol for extraction? Denatured ethanol is a form of ethanol that is diluted with other solvents such as acetone or...
What Are Aqueous Cleaning Solutions?
What are aqueous cleaning solutions? Aqueous cleaning solutions are water based cleaners that can be used for parts...
Reliable Acetone Manufacturers
Are you looking for reliable acetone manufacturers who can supply you with high quality chemicals and expert...
Company News
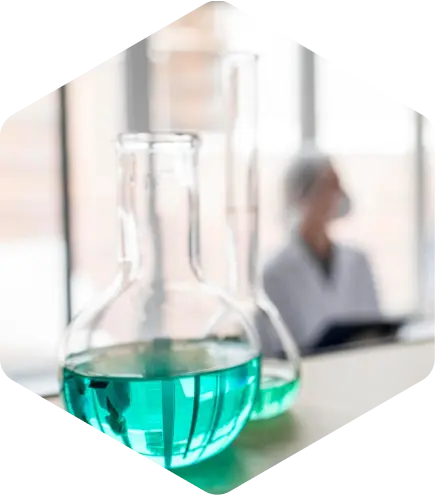
Managed Services
Discover the Latest in Safe and Sustainable Chemical Solutions
Stay informed with Ecolink’s blog! Subscribe now
Chemical Management Information
Stay updated with us
Sign Up for the Latest Updates
Stay informed about chemical supply chain disruptions and emerging innovations to keep your business at the forefront of efficiency and innovation. Uncover new ways to make your business practices more sustainable by incorporating safer products into your cleaning lineup.