Paint thinner is a versatile solvent with multiple uses and applications. The applications for paint thinners vary, from diluting to various paints....
Blog
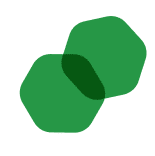
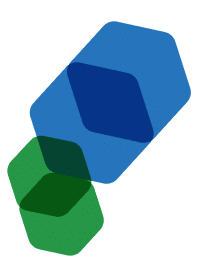
CHEMICAL INDUSTRY NEWS
Chemical Chat – Discover What’s New!
Bulk Chemical Suppliers For Industrial and Manufacturing Applications
Working with reliable bulk chemical suppliers is important for any industry that uses large amounts of chemicals and solvents for their day to day...
Is MEK Banned?
Methyl ketone ethyl (MEK) is a colorless and sweet-scented chemical with a toxic composition. It is because of its hazardous makeup, that its...
What Are Commodity Chemicals – Can You Purchase Commodity Chemicals In Bulk?
What are commodity chemicals? Commodity chemicals are the opposite of speciality chemicals that are used for niche...
Bulk Chemical Suppliers For Industrial and Manufacturing Applications
Working with reliable bulk chemical suppliers is important for any industry that uses large amounts of chemicals and...
Company News
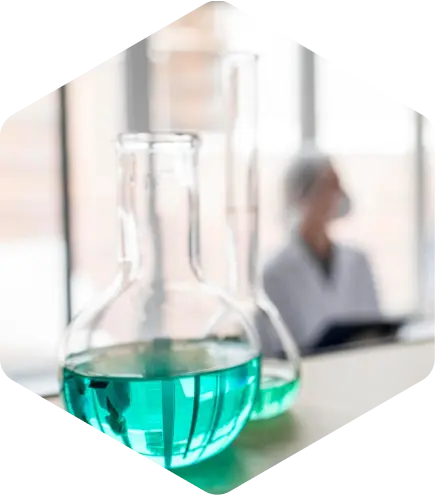
Managed Services
Discover the Latest in Safe and Sustainable Chemical Solutions
Stay informed with Ecolink’s blog! Subscribe now
Chemical Management Information
Stay updated with us
Sign Up for the Latest Updates
Stay informed about chemical supply chain disruptions and emerging innovations to keep your business at the forefront of efficiency and innovation. Uncover new ways to make your business practices more sustainable by incorporating safer products into your cleaning lineup.