Trichloroethylene, also known as TCE, is an organic solvent used in a variety of both industrial and commercial applications. Used by itself or as...
Blog
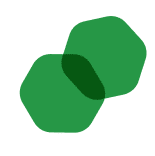
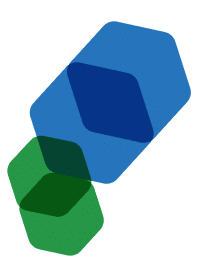
CHEMICAL INDUSTRY NEWS
Chemical Chat – Discover What’s New!
Turpentine vs Acetone
What are the differences when comparing turpentine vs acetone? Turpentine and acetone are similar chemical solvents that can be used for many of the...
Non Flammable Solvent Cleaner
Non Flammable Solvent Cleaner is generally considered the safer option for cleaning applications when compared to other solvents with lower...
How Is Methanol Produced?
How is methanol produced and what is it used for? Methanol (Methyl-Alcohol) is the simplest form of alcohol, commonly...
Turpentine vs Acetone
What are the differences when comparing turpentine vs acetone? Turpentine and acetone are similar chemical solvents...
Company News
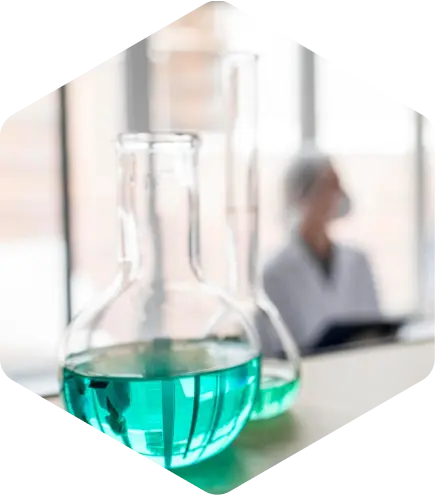
Managed Services
Discover the Latest in Safe and Sustainable Chemical Solutions
Stay informed with Ecolink’s blog! Subscribe now
Chemical Management Information
Stay updated with us
Sign Up for the Latest Updates
Stay informed about chemical supply chain disruptions and emerging innovations to keep your business at the forefront of efficiency and innovation. Uncover new ways to make your business practices more sustainable by incorporating safer products into your cleaning lineup.