Trichloroethylene, commonly referred to as TCE, has recently experienced a sudden increase in price. Though still widely used in the U.S. for...
Blog
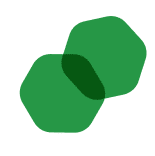
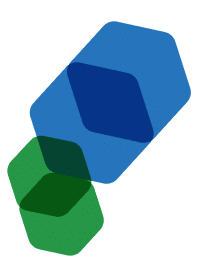
CHEMICAL INDUSTRY NEWS
Chemical Chat – Discover What’s New!
Rethinking Ink – Sydney Manns
We touch chemicals every time we go to the store—the cleaning wipes for the cart, the plastic packaging of foods, the grocery bags…but what about...
Sydney’s Internship Experience
The Ecolink internship gave me valuable life and career experience and ended up exceeding all of my expectations. Not only did I learn new skills,...
Getting to Know Sydney Manns
Getting to Know Sydney Manns Sydney Manns is a student at the University of Central Florida, studying English –...
Rethinking Ink – Sydney Manns
We touch chemicals every time we go to the store—the cleaning wipes for the cart, the plastic packaging of foods, the...
Company News
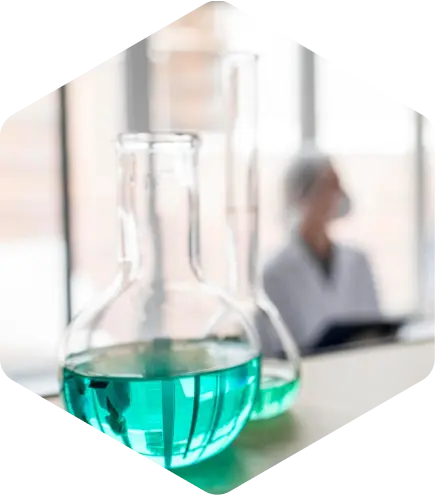
Managed Services
Discover the Latest in Safe and Sustainable Chemical Solutions
Stay informed with Ecolink’s blog! Subscribe now
Chemical Management Information
Stay updated with us
Sign Up for the Latest Updates
Stay informed about chemical supply chain disruptions and emerging innovations to keep your business at the forefront of efficiency and innovation. Uncover new ways to make your business practices more sustainable by incorporating safer products into your cleaning lineup.