Cooling water systems are often dependent on large quantities of water, often obtained from natural sources. This means that all sorts of...
Blog
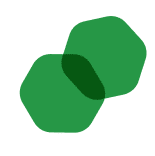
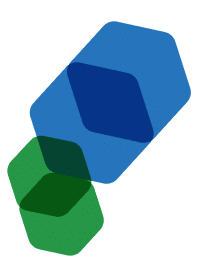
CHEMICAL INDUSTRY NEWS
Chemical Chat – Discover What’s New!
The Benefits of Concrete Slayer
Looking to Remove Concrete? As some industries know too well, concrete that has accumulated and hardened on surfaces where it is unwanted can be a...
Water Descaling Treatments
Water descaling treatments vary across the market and industry and at Ecolink we supply a number of water descaling chemicals designed to eliminate...
Difference Between Acetone And Acetate
What is the difference between acetone and acetate? To adequately explain the differences between acetone and acetate,...
The Benefits of Concrete Slayer
Looking to Remove Concrete? As some industries know too well, concrete that has accumulated and hardened on surfaces...
Company News
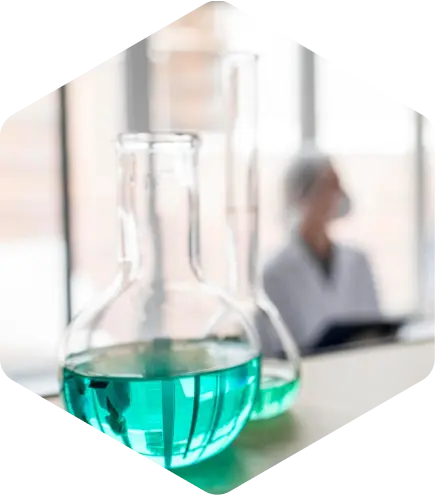
Managed Services
Discover the Latest in Safe and Sustainable Chemical Solutions
Stay informed with Ecolink’s blog! Subscribe now
Chemical Management Information
Stay updated with us
Sign Up for the Latest Updates
Stay informed about chemical supply chain disruptions and emerging innovations to keep your business at the forefront of efficiency and innovation. Uncover new ways to make your business practices more sustainable by incorporating safer products into your cleaning lineup.