VOCs, fully defined as Volatile Organic Compounds, are chemicals that evaporate with ease and are designed for versatility. However, even though...
Blog
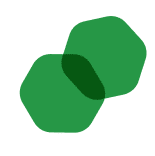
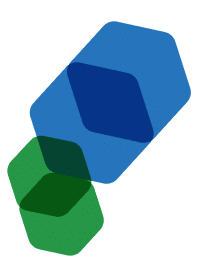
CHEMICAL INDUSTRY NEWS
Chemical Chat – Discover What’s New!
Understanding Commodity vs Specialty Chemicals
Chemicals and solvents are used in all industries for production, cleaning, and additive ingredients for everyday products, but what is the...
What Are Commodity Chemicals – Can You Purchase Commodity Chemicals In Bulk?
What are commodity chemicals? Commodity chemicals are the opposite of speciality chemicals that are used for niche markets and applications....
Scale and Corrosion Inhibitors
What are scale and corrosion inhibitors? These are concentrated chemicals that can be added to water to prevent...
Understanding Commodity vs Specialty Chemicals
Chemicals and solvents are used in all industries for production, cleaning, and additive ingredients for everyday...
Company News
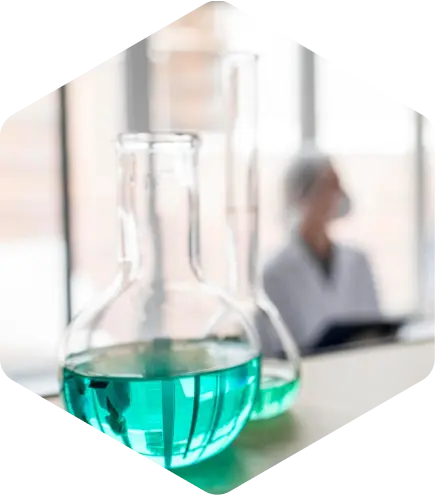
Managed Services
Discover the Latest in Safe and Sustainable Chemical Solutions
Stay informed with Ecolink’s blog! Subscribe now
Chemical Management Information
Stay updated with us
Sign Up for the Latest Updates
Stay informed about chemical supply chain disruptions and emerging innovations to keep your business at the forefront of efficiency and innovation. Uncover new ways to make your business practices more sustainable by incorporating safer products into your cleaning lineup.