Trichloroethylene, commonly referred to as TCE, is a popular halocarbon industrial solvent. The chemical is utilized in a variety of industrial...
Blog
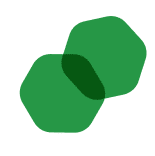
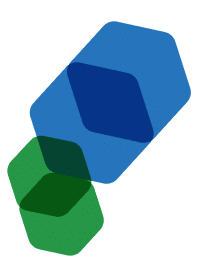
CHEMICAL INDUSTRY NEWS
Chemical Chat – Discover What’s New!
Corrosion Inhibitors For Closed Loop Water Treatment
Proper closed loop water treatment can prevent the build-up of scales and corrosion that can cause costly damage. Closed loops are used to heat and...
Water Treatment Chemicals
What are water treatment chemicals used for? Water treatment chemicals, also known as corrosion and scale inhibitors, are chemicals that can be...
Industrial Water Treatment Chemicals
Industrial water treatment chemicals are added to piping systems and machinery such as closed loops for water cooling...
Corrosion Inhibitors For Closed Loop Water Treatment
Proper closed loop water treatment can prevent the build-up of scales and corrosion that can cause costly damage. ...
Company News
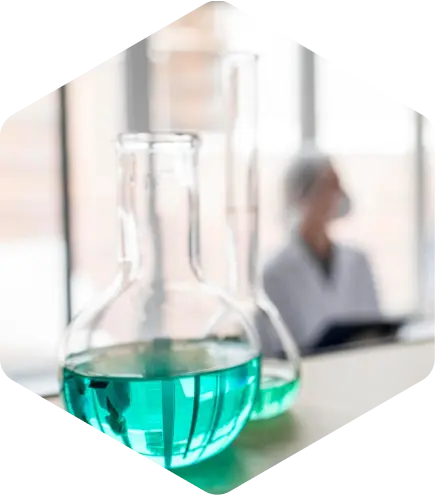
Managed Services
Discover the Latest in Safe and Sustainable Chemical Solutions
Stay informed with Ecolink’s blog! Subscribe now
Chemical Management Information
Stay updated with us
Sign Up for the Latest Updates
Stay informed about chemical supply chain disruptions and emerging innovations to keep your business at the forefront of efficiency and innovation. Uncover new ways to make your business practices more sustainable by incorporating safer products into your cleaning lineup.