Trichloroethylene, also known as TCE, is a controversial, yet widely used solvent for various industrial and commercial applications. However, using...
Blog
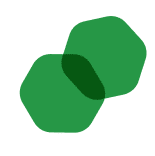
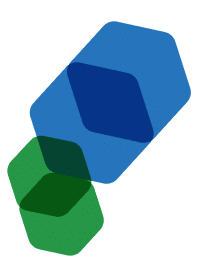
CHEMICAL INDUSTRY NEWS
Chemical Chat – Discover What’s New!
MEK Solvent vs Acetone
What is the difference between MEK Solvent vs Acetone? MEK is an acronym for Methyl Ethyl Ketone. According to the Center for Disease Control (CDC)...
How Is Methanol Produced?
How is methanol produced and what is it used for? Methanol (Methyl-Alcohol) is the simplest form of alcohol, commonly referred to by its chemical...
VOC Compliant Meaning
Why is it important to understand the VOC compliant meaning? VOC is an acronym for Volatile Organic Compounds....
MEK Solvent vs Acetone
What is the difference between MEK Solvent vs Acetone? MEK is an acronym for Methyl Ethyl Ketone. According to the...
Company News
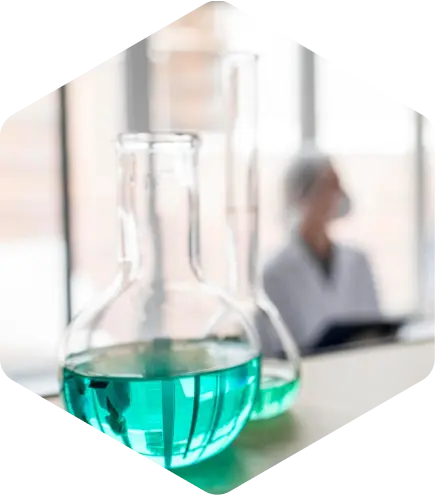
Managed Services
Discover the Latest in Safe and Sustainable Chemical Solutions
Stay informed with Ecolink’s blog! Subscribe now
Chemical Management Information
Stay updated with us
Sign Up for the Latest Updates
Stay informed about chemical supply chain disruptions and emerging innovations to keep your business at the forefront of efficiency and innovation. Uncover new ways to make your business practices more sustainable by incorporating safer products into your cleaning lineup.