What is TCE? TCE, also known as trichloroethylene, is a widely used organic solvent, present in both industrial and commercial applications. It is...
Blog
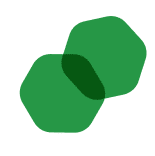
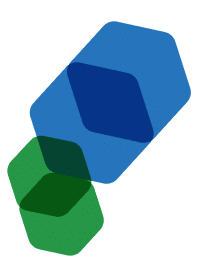
CHEMICAL INDUSTRY NEWS
Chemical Chat – Discover What’s New!
Difference Between Glycol And Ethylene Glycol
What is the difference between glycol and ethylene glycol? Encyclopedia Britannica defines Glycol as “any of a class of organic compounds belonging...
VOC Compliant Meaning
Why is it important to understand the VOC compliant meaning? VOC is an acronym for Volatile Organic Compounds. According to the United States...
Types Of Oxygen Scavengers
What are the different types of Oxygen Scavengers? For the purposes of understanding oxygen scavengers, an oxygen...
Difference Between Glycol And Ethylene Glycol
What is the difference between glycol and ethylene glycol? Encyclopedia Britannica defines Glycol as “any of a class...
Company News
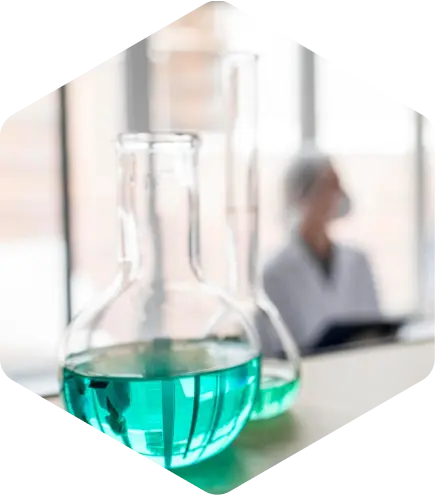
Managed Services
Discover the Latest in Safe and Sustainable Chemical Solutions
Stay informed with Ecolink’s blog! Subscribe now
Chemical Management Information
Stay updated with us
Sign Up for the Latest Updates
Stay informed about chemical supply chain disruptions and emerging innovations to keep your business at the forefront of efficiency and innovation. Uncover new ways to make your business practices more sustainable by incorporating safer products into your cleaning lineup.