Fouling refers to the buildup of solid matter in a water system, like scum on the surface of a pond, or rust on the hull of a boat. This buildup can...
Blog
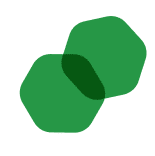
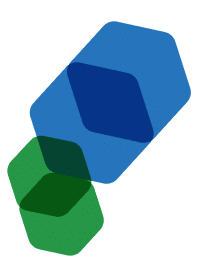
CHEMICAL INDUSTRY NEWS
Chemical Chat – Discover What’s New!
What Are Alkaline Degreasers?
What are alkaline degreasers? Curiously, pH is the measurement of the acidic or alkaline value of a substance or compound. Therefore to understand...
What Are Non-Butyl Degreasers?
What are non-butyl degreasers? Non-butyl degreasers are cleaning agents that are made without butyl ingredients or petrochemical additives....
Are Degreasers Acidic or Alkaline?
Are degreasers acidic or alkaline? The answer is both. Degreasers can be either acidic or alkaline. To distinguish...
What Are Alkaline Degreasers?
What are alkaline degreasers? Curiously, pH is the measurement of the acidic or alkaline value of a substance or...
Company News
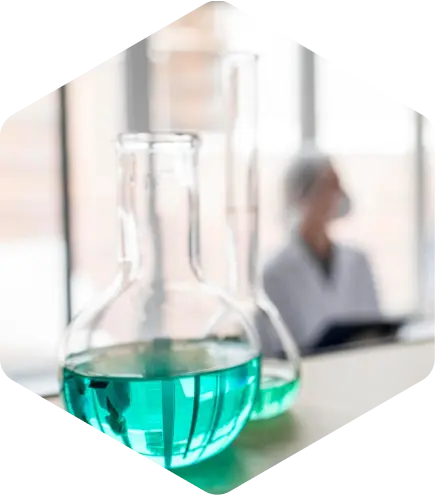
Managed Services
Discover the Latest in Safe and Sustainable Chemical Solutions
Stay informed with Ecolink’s blog! Subscribe now
Chemical Management Information
Stay updated with us
Sign Up for the Latest Updates
Stay informed about chemical supply chain disruptions and emerging innovations to keep your business at the forefront of efficiency and innovation. Uncover new ways to make your business practices more sustainable by incorporating safer products into your cleaning lineup.